杭州優質超臨界二氧化碳發泡廠家
發布時間:2022-02-21 01:30:28
杭州優質超臨界二氧化碳發泡廠家
近日,有網友在國家發展改革委官網留言詢問“’一次性發泡塑料餐具’是否包括‘可生物降解發泡塑料餐具’?比如用可生物降解的聚乳酸PLA發泡塑料材料制成的餐具,是否也在禁止之列?”發改委回答:“凡發泡塑料餐具均在禁止生產和銷售之列。”這份答復看似簡單,卻隱藏著數個值得深思的問題,深挖之下,細思極恐!1、一次性發泡塑料餐具 ≠ 一次性塑料餐具,可降解的一次性塑料餐具是否允許使用?國家發展委和改革委員會生態環境部發布的《關于進一步加強塑料污染治理的意見》中,關于一次性塑料餐具和一次性發泡塑料餐具有不同的規定:關于一次性發泡塑料餐具:禁止生產和銷售一次性發泡塑料餐具;關于一次性塑料餐具:到2020年底,全國范圍餐飲行業禁止使用不可降解一次性塑料吸管;地級以上城市建成區、景區景點的餐飲堂食服務,禁止使用不可降解一次性塑料餐具。到2022年底,縣城建成區、景區景點餐飲堂食服務,禁止使用不可降解一次性塑料餐具。到2025年,地級以上城市餐飲外賣領域不可降解一次性塑料餐具消耗強度下降30%。一次性發泡餐具:聚丙烯微孔發泡在飲食業和食品包裝業中,一次性發泡餐具使用為廣泛的材料是聚苯乙烯,通常采用含氯氟烴(CFC)或烴類(HC)發泡劑發泡,制成各種餐飲具如快餐盒、湯碗、方便面碗、生鮮托盤等。這些材料構成了嚴重的環境問題。中國曾于1999年、2005年以及2011年三次將一次性發泡塑料餐具列入工藝落后或產品落后目錄而遭淘汰。原因是:一些發泡餐具廠使用工業塑膠廢棄物作為原材料,摻雜少量的新料,再配一定量的滑石粉,生產出一次性發泡餐盒。盡管使用再生料生產發泡餐具有節約資源等優勢,但是來源不明的工業塑膠廢棄物存在眾多安全隱患和風險;發泡塑料餐具用完廢棄后難于回收利用;一次性發泡餐具對是否有雙酚A、苯乙烯單體、二聚體、三聚體、二噁英等毒性單體析出存在爭議;在生產過程中使用的發泡劑,有的會破壞大氣臭氧層,有的存在嚴重安全隱患。2013年2月26日,國家發改委發布第21號令,對《產業結構調整指導目錄(2011年本)》有關條目進行局部調整,其中之一便是在淘汰類產品目錄中刪除了一次性發泡塑料餐具(簡稱發泡餐具)。終,2020年1月16日發布的《關于進一步加強塑料污染治理的意見》明確禁止生產和銷售一次性發泡塑料餐具。一次性塑料餐具:一次性餐具按原材料來源、生產工藝、降解方式、回收水平分為以下三大類:1、生物降解類:如紙制品(含紙漿模塑型、紙板涂膜型)、食用粉模塑型、植物纖維模塑型等;2、光/生物降解性材料類:光/生物降解塑料(非發泡)型,如光生物降解PP類;3、易于回收利用材料類:如聚丙烯類(PP)、高抗沖聚苯乙烯類(HIPS)、雙向拉伸聚苯乙烯(BOPS)、天然無機礦物填充聚丙烯復合材料制品等。也就是說一次性發泡塑料餐具僅僅是一次性塑料餐具中的一個種類。禁止的是一次性發泡餐具,而不是完全禁止一次性塑料餐具,可降解的一次性塑料餐具是允許生產和銷售的。2、可生物降解的一次性塑料餐具是否需要“發泡成型”?采用的發泡劑是否同樣對環境有害?發泡是使塑料產生微孔結構的過程。幾乎所有的熱固性和熱塑性塑料都能制成泡沫塑料,常的樹脂有:聚苯乙烯樹脂、聚氨酯樹脂、聚氯乙烯樹脂、聚乙烯樹脂、脲甲醛樹脂、酚醛樹脂等。發泡劑:CFC發泡劑封閉于發泡材料中,它終將散逸、進入同溫層并參與消耗臭氧層的循環。再者,HC發泡劑一旦從泡沫中釋放出來,因具有光化學活性從而促使煙霧生成。因而,需要一種采用不參與破壞環境的化學反應的發泡劑發泡生產的可降解樹脂發泡材料。可降解餐盒使用材料分兩種:一種是天然材料制成的可降解天然材料餐盒,如紙制品、秸稈、淀粉等,可降解,也稱之為環保產品;另一種是以塑料為主要成分的可降解塑料餐盒,加入淀粉、光敏劑等物質制成(此類一次性餐盒的制造原料是可降解塑料,所謂可降解塑料就是在塑料的生產過程中加入一定量的添加劑,如光敏劑、淀粉等原料。這樣,可降解塑料制品在使用完,并廢棄在大自然中暴露三個月后,可由完整的形狀分解成碎片,因而至少在視覺上改善了環境。但這項技術的缺陷是,這些碎片不能繼續降解,只不過是由大片變成小片塑料,不能從根本上勝任消除白色污染的任務。發泡劑:CFC發泡劑封閉于發泡材料中,它終將散逸、進入同溫層并參與消耗臭氧層的循環。再者,HC發泡劑一旦從泡沫中釋放出來,因具有光化學活性從而促使煙霧生成。因而,需要一種采用不參與破壞環境的化學反應的發泡劑發泡生產的可降解樹脂發泡材料。目前,常用的可降解塑料聚乳酸(PLA)餐盒是需要發泡的,至于其他可降解塑料是否需要發泡,發泡劑是否污染環境,還需要更專業的解答,請在下方留言或掃描二維碼,分享您的觀點:按【姓名+公司名+職務】格式,發送備注3、如果《關于進一步加強塑料污染治理的意見》中禁止生產和銷售的超薄塑料購物袋、農用地膜,一次性塑料棉簽,塑料微珠全都使用可生物降解材料,是否允許生產和銷售?目前還沒有明確的答案,您怎么看?4、可降解塑料真的環保嗎?可降解塑料中也會使用發泡劑破壞環境,此外花費大量成本和時間使用可降解塑料,但可降解塑料混雜在傳統塑料中,無法回收利用,只能用傳統方法掩埋焚燒處理,究竟該使用可降解塑料還是建設塑料閉環,采用可回收性設計,這是一個值得思索的問題。

杭州優質超臨界二氧化碳發泡廠家
聚丙烯( PP) 珠粒發泡材料具有優異的耐熱、隔音、抗沖擊以及耐化學腐蝕等性能,近年來被廣泛應用在包裝、建 筑、汽車等行業。PP 在其熔點溫度附近的熔體強度會急劇下降,低熔體強度導致其難以得到好的泡孔結構,所以 PP 珠 粒發泡的技術難度大,目前只有少數國家掌握了 PP 珠粒發泡的技術,因此 PP 珠粒發泡的研究受到了國內外的廣泛關 注。文中從制備工藝、發泡裝備、性能改進、表征方法等方面綜述了近年來國內外 PP 珠粒發泡的研究動態,并對該領域 今后的研究方向進行了展望。聚丙烯(PP)珠粒發泡材料具有質輕、抗沖緩震、 耐腐蝕、隔熱隔音等優良的特性,與傳統的直接成 型工藝相比,PP 珠粒發泡的優勢在于它的自由成 型性,發泡珠粒均勻的尺寸與穩定的發泡倍率使其非 常適合模塑成型,可以生產具有復雜幾何結構以及高 維尺寸精度的制品。 早實現工業化生產的珠粒發泡產品是聚苯乙烯 發泡珠粒(EPS),其次是聚乙烯發泡珠粒(EPE)與聚 丙烯發泡珠粒(EPP)。其中,EPP 的熱穩定性要優 于 EPE,抗沖擊性能要優于 EPS,此外其耐老化、耐腐 蝕性也非常優異,是非常環保的材料,因此 EPP 被廣 泛應用于包裝、建筑、汽車等行業,特別是在汽車行業 的需求增長十分迅速。鑒于世界各國對 EPP 材料研究的重視,本文從 EPP 的生產工藝、裝備、性能改進以 及表征手段等方面介紹了近年來 EPP 的研究進展與 動態。聚丙烯微孔發泡 聚丙烯發泡珠粒制備聚丙烯發泡機理 PP 珠粒發泡的機理為過飽和氣體法。如 Fig. 1 所示,注入的發泡劑在高溫或高壓環境下溶解在聚合 物熔體中形成飽和的均相體系,然后通過快速卸壓或 者溫度驟升造成熱力學的不穩定來形成過飽和體系, 這個階段中 PP 基體與溶解在其中發泡劑發生相分 離,氣泡開始成核并大量生長,穩定后經冷卻定型成為 發泡珠粒。聚丙烯發泡珠粒的生產方法 目前工業化生產 EPP 的工藝有 2 種:一種是以日 本的 JSP 株式會社與 Kaneka 公司為代表的反應釜 法,反應釜法也是目前應用廣泛的 EPP 的工業化生 產工藝;另 一 種 是 以 德 國 Berstorff 公 司 與 BASF 公 司等為代表的擠出法工藝,相對于工藝成熟的反應 釜法而言,擠出法目前工業化并不廣泛。反應釜法: 反應釜法是將 PP 顆粒與助劑混合 造粒后放入反應釜中,升高溫度并通入物理發泡劑使 釜內壓力升高,在一定的發泡溫度下保壓一段時間后 打開泄壓閥門快速卸壓即得到發泡珠粒。根據反應釜 中分散介質的不同,又可分為無水法與有水法 2 種:前 者的反應釜中不加入液體的分散介質,PP 顆粒會堆積 在一起使發泡劑難以均勻溶解到每個顆粒中,所以為 了使發泡劑更好地溶解,釜內壓力一般需要在 10 MPa 以上;后者是先將 PP 顆粒分散在水中,發泡劑能均勻 溶解在 PP 顆粒中,所需壓力約2 ~ 6 MPa。反應釜法 的優點是工藝條件容易控制、發泡倍率高、泡孔結構 好、可二次發泡,缺點是間歇式生產導致成本較高。 日本 JSP 公司的專利介紹的生產工藝能夠生產 密度低于 0. 045 g /cm3 、平均泡孔直徑為 200 μm 的 EPP。這種方法是將尺寸均一的顆粒加入反應釜中, 升溫到稍低于發泡的溫度,保溫一段時間后再升溫到 發泡溫度,繼續保溫一段時間,打開高壓釜放出分散體 到大氣中,放出物料的同時繼續通入氮氣使釜中壓力 保持在放出物料前的壓力。后將得到的發泡珠粒洗 滌、離心分離后在空氣中靜置老化,這是目前工業化 成熟的 EPP 生產工藝。改進生產設備的結構也能在一定程度上改善 EPP 的 性 能。Hossieny 等 采 用 CO2 為 發 泡 劑 用 Fig. 2 中的實驗設備制備了 EPP,該設備在反應釜下端加裝了一個排料口模,卸壓時 PP 通過排料口模進入 收集裝置中,實驗研究了發泡過程中的泡孔形態與熔 融、結晶行為以及口模長度對發泡倍率的影響。結果 表明,由于熔融雙峰中的高溫熔融峰區域焓值的減少, 增加飽和壓力會提高發泡珠粒的體積膨脹比,密度降 低;而增加口模的長度則會減小其體積膨脹比,密度增 加。 國內武漢德冠新材科技有限公司開發出了實驗室 用商品化的釜壓發泡系統,發泡系統結構分反應釜 與收集釜,資料顯示能制備出發泡倍率8 ~ 60倍的發泡 珠粒。 如何拓寬 PP 的發泡溫度區間以及壓縮釜壓發泡 流程的時間也是研究的重點方向。丁杰等采用 CO2 作發泡劑,用 Fig. 3 中的無水法發泡裝置制備了 小泡孔直徑 為 9. 55 μm,泡 孔 密 度 小 于1. 5 × 109 cm - 3 的 EPP。其工藝改進在于在降溫到發泡溫度的 過程中保持釜內飽和壓力不變,恒溫一段時間后再放 出珠粒進行冷卻,其 PP 的發泡溫度區間約50 ℃,工藝 流程時間約為 2. 5 h反應釜法重要的工藝在于要使發泡劑能充分 溶解到 PP 顆粒中,所以其關鍵控制條件有反應釜的 溫度、壓力以及保壓時間等,適當地延長保壓時間與增 大壓力能有效促進發泡劑的溶解。目前反應釜法的工 藝已經比較成熟,但其高成本也限制了 EPP 的廣泛應 用,探索新的生產工藝條件和生產裝備來降低其成本 是今后研究所需解決的問題。擠出法: 擠出法生產 EPP 是在傳統擠出發泡 裝置后連接一個水下切粒裝置,如 Fig. 4 [14]。PP 顆粒 與發泡劑等助劑經過擠出機均勻混合后在口模出口處 由于壓力驟降而發泡,發泡的材料通過水下切粒裝置被切割定型成尺寸均一的發泡珠粒。擠出法可連續生 產、效率高、珠粒尺寸均勻,缺點是生產過程中的工藝 參數難以控制,此外由于 PP 在溫度低于熔點時幾 乎不流動,而當溫度高于熔點后,熔體強度又急劇下降,所以適宜的發泡溫度區間很窄(約為 4 ℃ ),擠 出法對 PP 的熔體強度要求較高,一般要用改性的熔 體強度較高的 PP,這些缺點限制了擠出法的應用與發 展。 德國 Berstorff 公司研發的 Schaumex ○RBEADS 生 產線是目前比較成熟的擠出法生產發泡珠粒的工藝。 采用丁烷作發泡劑,高熔體強度聚丙烯(HMSPP)為原 料,可以生產發泡倍率約 60 倍,直徑為3 ~ 5 mm,密度 為15 ~ 100 kg /m3 的 EPP 。 在 PP 中加入無機填料能夠增強 PP 的熔體強度, 得到更 好 的 泡 孔 結 構,從 而 改 進 EPP 的 性 能。Nofar [18]等采用 5% 的超臨界 CO2 作發泡劑,用單螺桿擠 出發泡加入了納米粘土的均聚線性聚丙烯( LPP),得 到了發泡倍率為 20 倍,泡孔密度為108 ~ 109 cm - 3 的發 泡材料。實驗表明,納米粘土的加入不但能夠顯著改 善 LPP 的熔體強度,降低其擠出發泡的工藝難度,還 能夠增加氣泡成核點,誘導發生異相成核,從而得到泡 孔密度、體積膨脹比都較大的 EPP。與德國 Berstorff 公司的單階擠出系統相比,雙階 擠出系統能夠使 PP 與發泡劑得到更好的塑化與混 合,此外還能夠更好的控制擠出發泡過程中各階段的 溫度,缺點是設備成本較高。Lee [19]等采用 Fig. 6 中的 雙階擠出系統,用不同劑量的超臨界 CO2 (Wt = 1% , 3% ,5% )作發泡劑擠出發泡非交聯的 HMSPP,研究表 明,擠出發泡的倍率與熔體溫度呈“山”形關系,此外 終的泡孔密度與發泡倍率會隨著釋壓速率的增大而 增加。另外,隨著 CO2 注入量的增加,聚丙烯發泡材 料的體積膨脹比增加,但泡孔密度則是先增大后減小。擠出法生產 EPP 作為連續、高效的生產工藝,是 今后 EPP 生產的發展方向。目前需要解決的問題在 與開發適用于擠出發泡的低成本高熔體強度的 PP,此 外新型物理發泡劑超臨界 CO2 的應用也是今后的發 展方向,超臨界流體發泡劑的高溶解性可以縮短聚合物/氣體體系的飽和時間,增加成核密度,得到微孔的 發泡材料。其中超臨界 CO2 的實現條件(t c = 30. 98 ℃ pc = 7. 4 MPa)是接近聚丙烯發泡條件的超臨界 流體發泡劑,此外其還具有無毒、不易燃、化學惰性等 優點,近年來受到了廣泛的關注,是替代傳統化 學發泡劑的選擇。聚丙烯發泡珠粒改性PP 泡沫材料由于使用場合的不同,對性能的要求 也不同,例如包裝材料需要良好的抗沖緩震性能,建筑 材料則需要良好的隔音、隔熱性能,而汽車部件則需要 更好的剛性等,通常需要對 EPP 的性能進行改進來適 應不同的需求。改進 EPP 性能的方法有 2 種:一是改進生產工 藝,二是對 PP 原料進行改性。前者主要是通過改進 生產中的工藝流程、控制條件或者發泡裝備等來改進 EPP 的性能,這些手段可以有效地調節 EPP 的結構與 形態,有利于得到泡孔直徑更小、發泡倍率越大的產 品,但由于對材料本身的改變不大,所以對 EPP 力學 性能的改善作用有限;而后者則是通過改性 PP 原料 進而改進終的 EPP 產品的性能,PP 的改性方法主要 有化學交聯、物理共混、熔融支化等,通過對原料的改 性,不但能夠提高其熔體強度、降低其發泡難度、得到 更好的泡孔結構,同時也能有目的地改進 EPP 的力學 性能,所以 PP 的改性也是目前研究的熱門方向。為了提高 EPP 的發泡倍率與彈性、改善其緩沖性 能,日本 Kaneka 公司改進了釜壓生產工藝。首先 在顆粒從反應釜中放出之前提高釜內的壓力,其次是 將顆粒從反應釜中放出的同時使其與飽和蒸汽充分接 觸;前者使顆粒的受力增加,避免了顆粒在管道中粘 結,此外反應釜內蒸汽的閃蒸作用有助于顆粒的進一 步膨脹,后者會使顆粒的冷卻速率變緩,顆粒表面與內 部充分冷卻凝固,提高珠粒的尺寸穩定性。此工藝可 以制備密度為 0. 11 ~ 0. 30g /cm3 ,發泡倍率為30 ~ 60, 閉孔含量為 90% ,泡孔尺寸為150 ~ 300 μm 的 EPP。將 PP 與無機物或者某些塑料基體共混是常用 的改性方法,丁杰等研究了納米碳酸鈣的加入對 EPP 的影響,納米碳酸鈣的比表面積大,在發泡過程在 能起到異相成核的作用,從而使 EPP 的泡孔密度增 大,泡孔直徑減小;但同時也會使 PP 的發泡溫度區間 變窄。Zhang 等分別用 3 種多官能團單體———己二 醇二丙烯酸酯(HDDA)、三烯丙基異氰脲酸酯(TAIC) 與季戊四醇四甲基丙烯酸酯(PETMA)來改性聚丙烯, 并用偶氮二甲酰胺(AC)作發泡劑發泡改性 PP。實驗 表明三者都能使聚丙烯出現接枝或者交聯結構從而增 強線性聚丙烯的熔體強度,對比而言,HDDA 改性的聚 丙烯發泡效果好,其泡孔的結構尺寸以及發泡倍率 都較好。
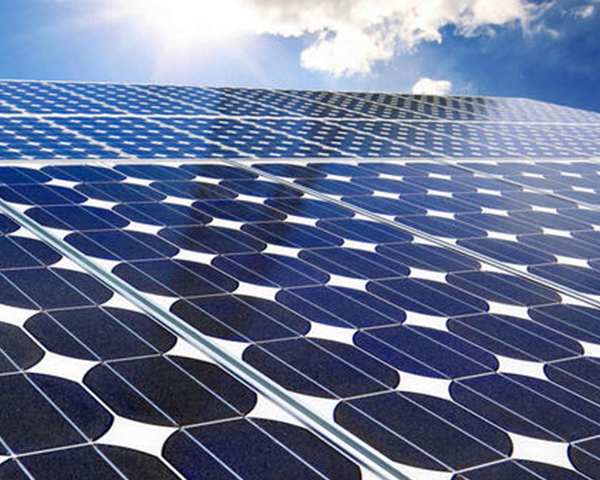
杭州優質超臨界二氧化碳發泡廠家
摘要:采用不飽和聚酯對線型均聚聚丙烯進行熔融接枝改性。改性后的聚丙烯形成了一種微交聯結構,其中凝膠含量約為10%,且凝膠的交聯點之間平均相對分子質量達到3.0×105。這種微交聯的聚丙烯和未改性的線型聚丙烯相比,具有相近的剪切黏度和熔體流動速率,但熔體彈性明顯增加,且有應變硬化行為,其拉伸黏度是本體聚丙烯的10倍。因此,微交聯結構的引入改善了聚丙烯的發泡性能。以超臨界二氧化碳為發泡劑,在不加入成核劑的條件下,得到了泡孔密度為1.1×109cm-3的微孔泡沫塑料。普通線型聚丙烯發泡的溫度區間只有4℃。因此,普通線型聚丙烯須經過改性提高熔體強度,使氣泡核增長時泡孔結構可以維持到結晶過程的發生。通常有4種方法提高聚丙烯的熔體強度:增加聚丙烯的相對分子質量,拓寬相對分子質量分布(或者引入超高分子量尾端),引入長支鏈結構以及形成交聯結構。其中長支鏈的引入雖然改善了PP發泡性能,但是會引起線型聚丙烯成核速率降低,在制備高泡孔密度的泡沫時,必須加入納米成核劑。而Zha和Xing的研究結果顯示以超臨界二氧化碳為發泡劑利用交聯聚烯烴制備發泡材料時,在沒有使用成核劑的條件下,均得到了高泡孔密度的泡沫材料。雖然交聯結構的引入可以明顯改善聚丙烯的發泡性能,但同時也使得聚丙烯的剪切黏度大幅上升,引起加工困難,并由于三維網絡結構的存在使得發泡塑料無法回收再利用,應用上受到限制。近年來一些學者發現在聚烯烴中可以引入“微交聯”結構,在保持聚烯烴原有的剪切黏度下,提高聚烯烴的熔體彈性和拉伸黏度,并改善聚烯烴發泡性能。本文采用一種自制的不飽和聚酯對線型均聚聚丙烯進行熔融接枝改性,在聚丙烯中引入微交聯結構,并且對形成的微交聯進行了表征,同時測試了改性聚丙烯的流變行為。后利用超臨界二氧化碳在高壓釜內對改性聚丙烯的發泡性能進行了評價。聚丙烯微孔發泡實驗部分1.1 試劑與儀器線型均聚聚丙烯PP T36F:重均相對分子質量(-Mw)=292050,相對分子質量分布寬度(MWD)=4.2,熔體指數(MFI)=2.5,齊魯石化公司;不飽和聚酯(ULP):-Mn=1700~2500,自制;過氧化二異丙苯(DCP):純度99%,苯乙烯(St):純度99%:上海化學試劑廠;二氧化碳:純度99%,上海凌峰試劑廠。平板旋轉流變儀Thermo Hakke6.0和密煉機Haake Rheocord90型:Thermo Scientific公司(德國);ARES旋轉流變儀:TA Instrument 公司(美國);掃描電鏡:型-JSM-6360LV,日本電子公司(日本)。1.2 實驗過程聚丙烯的改性:不飽和聚酯的結構參見Fig.1。聚丙烯改性按以下步驟進行:稱取PP粒料100.0g、不飽和聚酯2.5g、過氧化二異丙苯0.1g和苯乙烯2.0g,混合,加入密煉機中,170℃,轉速30r/min的條件下,熔融反應6.0min。然后停止攪拌,在氮氣氣氛下170℃熱處理15min。反應過程大致如Fig.2。聚丙烯的發泡過程:將高壓釜用CO2沖洗后,放入5gPP樣品。關閉高壓釜,充入CO2使釜內壓力達到6MPa。高壓釜在油浴中升溫至170℃,維持30min以保證聚丙烯熔融和CO2溶解在聚丙烯內。緩慢調節壓力至所需要發泡壓力15MPa,保持30min后,迅速打開閥門泄壓,并將高壓釜放入冰水混合物中冷卻后取出發泡樣品。結果與討論2.1復數黏度2種PP樣品的復數黏度隨角頻率的變化見Fig.3。2條基本相重合的曲線表明引入的微交聯結構并沒有引起改性PP黏度增加。為了比較2種PP剪切黏度的變化,通過Cross方程對兩曲線進行擬合。從Tab.1中可以看到,交聯改性并沒有引起改性后聚丙烯零剪切黏度的急劇增加,且熔體指數略有下降,這主要是因為微交聯結構交聯點間的平均相對分子質量達到了3.0×105,遠高于聚丙烯的臨界纏結相對分子質量(5600)。但由于微交聯而形成的三維網絡結構,使得熔體松弛時間和熔體彈性增加,所以改性后PP的特征松弛時間卻增加為原來的7.4倍。而剪切變稀指數從0.55降為0.46,剪切變稀行為有所減弱。2.2儲能模量和損耗角根據線性粘彈性理論,在末端低頻率區域,只有長的松弛時間對熔體的低頻末端儲能模量有貢獻,所以儲能模量和末端角頻率有以下的關系:Fig.4(A)顯示,改性后PP的儲能模量為未改性PP的2倍,儲能模量曲線末端的斜率也從1.51下降到0.87,改性后PP的熔體彈性明顯增強。損耗角同樣對熔體彈性的改變很敏感。Fig.4(B)顯示,未改性PP損耗角的正切值曲線隨角頻率減小而迅速抬升,而改性后PP損耗角正切值在低頻末端區緩慢變化并趨于平緩。相同頻率下損耗角正切值越小,熔體彈性行為越明顯。Winter和Chambon的研究表明,在臨界凝膠點,損耗角正切值為一常數與角頻率無關,并符合以下比例關系:式中:n———松弛指數。Fig.4(B)中損耗角正切值與角頻率還存在一定的依賴關系,鄭強等在研究過氧化物交聯的低密度聚乙烯的體系中也發現了這種現象,并認為是由于測試的非平衡態導致了這一情況的發生。2.3 法向應力差聚合物熔體受到剪切作用時,由于法向應力差的的作用,呈現彈性行為。通過比較法向應力差,可知聚合物熔體彈性的大小。采用定剪切速率掃描法來測試改性前后PP熔體彈性行為的改變。由Fig.5可以看到,改性后PP的法相應力差明顯提高,熔體彈性增強。2.4 瞬時拉伸黏度Fig.6是在應變速率接近發泡時拉伸應變速率0.1s-1時,2種PP的瞬時拉伸黏度隨應變變化的曲線,圖中虛線是線型聚丙烯3ηo曲線。由于拉伸應變速率較大,純PP的拉伸黏度曲線在還沒有進入穩態流動區域前就已經斷裂,且沒有應變硬化現象發生。而改性PP有明顯的應變硬化行為,瞬時拉伸黏度向上抬起偏移了3η0曲線,大瞬時拉伸黏度是純PP的10倍,達到5.6×105Pa·s。交聯點之間的鏈段被拉伸是改性聚丙烯發生應變硬化行為的原因。2.5 發泡行為應變硬化行為對聚丙烯發泡性能有重要的影響。采用超臨界二氧化碳為發泡劑,在反應釜中考察了改性PP的發泡性能。工藝條件為溫度170℃、壓力15MPa。從Fig.7A中可以看到,純PP發泡后呈現大部分的未發泡區域和一些串孔的泡孔,基本沒有可見的泡孔結構。說明純PP的熔體強度不夠,無法支持發泡時氣體擴散引起的膨脹應力,在泡孔沒有進入固化和定型階段時,PP熔體氣泡壁已經破裂。Fig.7B中顯示,改性PP發泡后,可以看到細密的氣泡孔布滿整個橫截面,泡孔呈現出多邊形的結構。利用圖形分析軟件分析得到的泡孔大小和泡孔密度列在Tab.2。改性后微交聯PP的泡孔直徑在10μm右,泡孔密度達到1.1×109cm-3。微交聯使得改性PP具有應變硬化行為,不僅增加了PP的熔體強度,同時熔體在承受拉伸應力時,熔體形變變得均勻,使得熔體不容易斷裂,因此改性PP的發泡性能得到明顯改善。非常高的泡孔密度也說明發泡時有很高的成核速率,具體原因尚需更多的研究。利用不飽和聚酯對線型聚丙烯進行了熔融接枝改性,得到一種具有微交聯結構的聚丙烯。這種微交聯的聚丙烯在顯著增加聚丙烯的熔體彈性以及拉伸黏度的同時,沒有使剪切黏度劇烈增加,使得在改善發泡性能的同時,保持了聚丙烯的加工性能。改性后的PP以超臨界CO2為發泡劑發泡,在不加入任何成核劑的條件下,可以得到發泡倍率25.6倍,泡孔密度1.1×109cm-3的微孔泡沫塑料。

杭州優質超臨界二氧化碳發泡廠家
新型微孔發泡聚丙-烯-材料(簡稱MPP),大家都在找惠州東銘新能源材料股份有限公司,10多年行業經驗,口碑好,廣東地區實力生產廠家。惠州東銘新能源材料股份有限公司具備雄厚的研發實力、完善的產品認證體系(包括國內外)、全覆蓋的銷售網絡和有機硅材料上下游完整的產業鏈,能夠為新能源產業的客戶提供完善的解決方案!微孔發泡聚丙-烯-材料MPP的特點及優勢:聚丙烯微孔發泡 (1)同等發泡倍率(或表觀密度)下,由于泡孔尺寸較小,微孔發泡材料的機械性能損失較小。這意味著使用MPP可以更加節約材料,更加降低制品重量和體積。(2)由于泡孔尺寸在1-100μm之間可控,MPP可以被剖切成厚度小于0.1mm的超薄片材,而片材表面不會穿孔,可應用于微電子器件的包裝。(3)由于表面大量微米級泡孔的存在,MPP適合作為液晶顯示器背光模組的反射板,提高漫反射率。(4)微米尺度的泡孔有效降低了泡孔內氣體的對流,從而有效降低了由空氣對流引起的熱傳遞。因此高倍率的微孔發泡材料具有依賴于泡孔結構的長期穩定的低導熱系數。(5)輕質高強的MPP片材適合于作為揚聲器振膜使用。(6)同樣由于其微米尺度的泡孔,MPP具有極-佳-的表面保護性能,可應用于液晶面板等防護性要求較高的包裝領域。
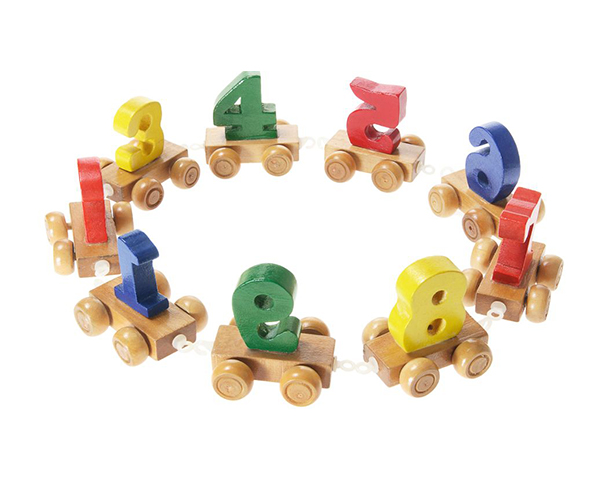
杭州優質超臨界二氧化碳發泡廠家
核心技術優勢:1、技術創新:·成套設備:自主研發的超臨界CO2微孔發泡成套裝備,將化學工程的技術手段應用于聚合物加工。·適用性好:工藝適用于多種聚合物材料的微孔發泡(PP、PA、TPU、TPAE、PVDF…)。·控制確:通過宏觀工藝參數(溫度、壓力)的確控制,實現了對泡孔結構的確控制。2、性能優勢:·多類別:從彈性體到工程塑料的多種聚合物輕量化材料產品 。·高性能:充分發揮多孔結構作用能并配合材料的功能化改性,實現材料的高性能化 。·輕量化:低密度(min) 30kg/m3 。重環保:純物理發泡,制程清潔環保,產品安全無毒。聚丙烯微孔發泡已實現量產的產品種類:1、M-PP:聚丙烯微孔發泡板材2、M-PVDF:聚偏氟乙烯微孔發泡板材3、M-PA12:尼龍12微孔發泡板材4、M-TPU:熱塑性聚氨酯彈性體微孔發泡板材5、M-TPEE:熱塑性聚酯彈性體微孔發泡板材6、M-PEBA:熱塑性聚酰胺彈性體微孔發泡板材

杭州優質超臨界二氧化碳發泡廠家
塑料部件在國內汽車上占重量的10%左右,在國外汽車上達到了15%至20%。微孔發泡技術能使塑料部件的重量降低15%至30%,廣泛應用于儀表板、電機支架、座位板、空調風罩、門嵌飾板等內外飾。聚丙烯使用量占比塑料部件50%以上。讓汽車用上更多的塑料部件,還有很多功課可以開展。全球微孔發泡相關的專利申請,前三位為:美國、日本、德國。Trexel公司的MuCell技術是目前為成熟、商品化為廣泛的微孔發泡技術,該技術來源于麻省理工學院在20世紀80年代提出的發明專利。Trexel公司在1995年通過專利權轉讓獲得這項技術的全球開發和商品化推廣,并在此基礎上開發出連續微孔成型技術--MuCell。MuCell技術的核心即采用超臨界流體為發泡劑,發泡劑在聚合物中形成均勻分布的微小氣孔,通過壓力控制氣泡的生長使樹脂形成泡孔均勻的微孔結構。聚丙烯微孔發泡微孔發泡技術讓汽車駛向輕量化——在汽車非金屬部件的輕量化領域,微孔發泡材料是行業競相研究的主要課題之一。2018年,中石化就將聚丙烯微孔發泡材料應用技術開發列為重點課題。國內微孔發泡材料注重原料技術研發。在高校方面,北京化工大學在微孔發泡工藝的專利申請量上占有主要地位,主要發明人為楊衛民課題組和何亞東課題組。楊衛民課題組的研究方向主要是微孔發泡專用注射機的結構改進,在專利申請方向上側重于改進螺桿結構和設置滲透釜來獲得聚合物熔體/超臨界氣體均相體系。近期,華東理工大學化工學院趙玲教授領銜的“高性能聚丙烯微孔發泡材料綠色制備過程的優化和強化”項目斬獲上海市科技進步獎一等獎。北京化工大學教授、教育部“長江學者獎勵計劃”特聘教授楊衛民,華東理工大學化工學院院長、聯合化學反應工程研究所所長、教育部“長江學者獎勵計劃”特聘教授趙玲,兩位教授將出席“2020中國聚烯烴大會”,并介紹聚烯烴發泡技術與材料開發。國內汽車產業節能減排發展趨勢愈加顯著,對汽車輕量化提出了更高要求。特別是在車市持續萎靡、新能源汽車競爭愈發激烈的情況下,輕量化成為汽車產業從困境中突圍的重要方向。整車廠、改性塑料企業都在加大輕量化材料領域的布局。汽車輕量化要求更高,對聚丙烯微孔發泡材料的需求正在進一步放大!在這個領域有哪些新的進展和要求?有哪些新的技術研發?趙玲教授將在“2020中國聚烯烴大會”開講。