安徽聚乳酸發泡材料定制
發布時間:2025-02-27 00:52:19
安徽聚乳酸發泡材料定制
PBAT是一種石油基生物可降解塑料 PBAT材料不僅可堆肥也可以生物降解,PBAT生產的生物降解材料是生物堆肥垃圾中心回收生物變廢物時的使用材料,。主要應用于:全降解包裝袋,全降解包裝用薄膜,物品內襯,盒子內托,食品包裝袋等。那么,生物基塑料和生物可降解塑料到底是什么?生物基塑料強調塑料制品的原材料,因此未必具有生物可降解性能。而生物可降解塑料則強調塑料制品的廢棄處理方式(可否分解),這類塑料未必是生物基的,它也可以是化石基的。在歐洲,可堆肥塑料(生物可降解塑料)有完善的法例約束(歐洲標準EN 13432)。要落實可持續的塑料政策,就得推行生物垃圾的分類收集,并努力發展工業堆肥,而非僅僅紙上談兵。大力發展可堆肥塑料,除了要防止其被廢棄在自然環境中,還應該把它們集中工業堆肥,形成塑料處理的“閉環”。可堆肥塑料雖然被認為是良好的一次性塑料替代品,但它有局限性。其局限性在于可堆肥塑料仍然是基于“用完即棄”的邏輯,而非可反復使用的材料。因此,我們依然將反復使用模式作為主要的塑料政策進行倡導。寧波致微新材料科技有限公司成立于2017年是一家專注于研究、開發、生產及銷售的高科技企業,其中推出的PBAT材料,發泡出應用在禮品內襯、內托包裝盒中等等,在超臨界物理發泡下使材料做到了無毒、無味、無化學物質殘留,其表面光滑,質感細膩,可印刷,耐摔耐折疊等。
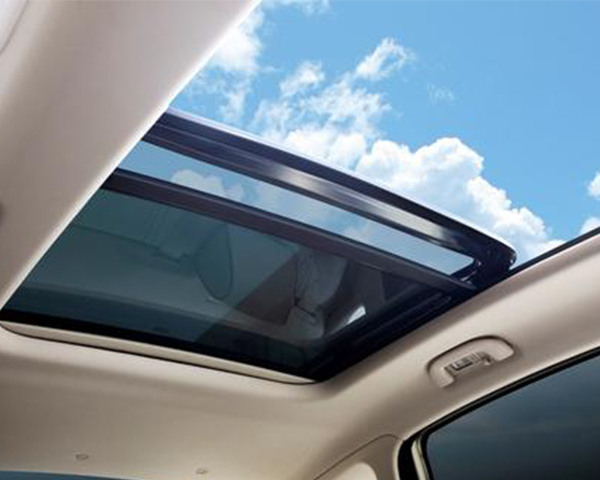
安徽聚乳酸發泡材料定制
利用化學改性非交聯法和單螺桿擠出機,采用一步法擠出工藝研制了汽車內飾用聚丙烯(PP)微發泡料。以均聚PP和共聚PP為基礎樹脂,考察了影響PP發泡的主要因素(如引發劑、發泡劑的用量、擠出溫度等)。結果表明,具有良好性能的PP微發泡專用料的配方(質量份數):均聚PP為40.00份,共聚PP為60.00份,過氧化二特丁烷為0.18份,過氧化二異丙苯為0.02份,改性劑為0.50份,碳酸鈣為0.50份,發泡劑AC為 0.40份。以其制備的微發泡片材泡孔直徑小于50μm,泡孔密度可達個/cm3。關鍵詞: 聚丙烯 微發泡 汽車內飾件 專用料 聚丙烯(PP)發泡材料具有質輕、耐高溫、綠色環保、易注射成型、成型周期短和成本低等優點。隨著汽車輕量化的發展,PP發泡材料在汽車內飾件上的應用越來越多。普通 PP發泡制品表觀質量不理想,僅適用于需表面附皮的高端車,汽車用PP發泡材料主要為質量更好的 化學微發泡材料[1-3]。化學微孔發泡材料的泡孔是直徑為十幾到數十微米,封閉微孔泡以小于50μm 為佳。目前國內行業實際生產水平大多在80~350μm,國外也只有美國、意大利、日本等少數幾個國家能生產。本工作利用化學改性非交聯法,以均聚PP和共聚PP共混物為基礎樹脂,采用一步法工藝研制出了性能符合相關指標要求的汽車內飾件用 PP 低 倍微發泡專用料,以其制備的微發泡片材泡孔直徑小于50μm,泡孔密度可達個/cm3。聚丙烯微孔發泡1 試驗部分1.1 主要原料 均聚PP(記作 PP1),熔體流動速率(MFR)為3.0g/(10min),中國石化齊魯分公司;共聚PP(記作PP2),MFR為2.0g/(10min),中國石化齊魯分公司;抗氧劑,168和1010,上海汽巴高橋化學有限公司;過氧化二特丁烷(DBP),過氧化二特丁烷(DBP),過氧化二異丙苯(DCP),二乙烯基苯,偶氮二甲酰胺(發泡劑AC),液體石蠟,江蘇強盛功能化學股份有限公司;發泡改性劑DMS-10,自制。1.2 儀器設備 RC300C型轉矩流變儀,德國HAAKE公 司;CMT450料試驗 機,天水三斯有限公司;∮25單螺桿擠出機,德國BRABENDER公司;AH-2奧林巴斯顯微鏡,日本奧林巴斯公司。1.3 試樣制備工藝 混料:將樹脂、過氧化物、改性劑、抗氧劑、成核劑和發泡劑按配比稱量,投入10L高速攪拌機,低速混合1min,高速混合2min出料,料溫不 高于50℃。擠出發泡:擠出機設置溫度180~200℃,機頭溫度195℃,距機頭30cm 處加壓輥將發泡片壓平,取樣待用。1.4 測試表征拉伸強度按照GB/T1040.3—2006測試,采用4型試樣,拉伸速度為50mm/min;彎曲強度和彎曲模量按GB/T9341—2000測試,寬度25mm;沖擊強度按GB/T1843—2008測試;表觀密度按GB/T6343—2009測試;泡孔密度按方法測試。2 結果與討論.1 引發劑的選擇以PP1/PP2質量 比2/3共混物做基礎樹脂,DBP和DCP不同配比的混合物0.2份做引發劑,測試體系的熔體強度和觀察發泡片質量,結果見表1。DBP/DCP對發泡片表面質量的影響 注:擠出口模厚度0.6mm,寬度50mm。由表1看出,DBP和DCP都能提高PP熔體強度,但片材表面和泡孔均勻性不同,隨DCP含量增加,擠出片材表面質量變差,泡孔變得不均勻;DCP雖有利于提高熔體強度,但比例不宜過大,以不超過引發劑總質量分 數20%為宜。這是由于DCP分解溫度低于PP加工溫度,擠出反應時,DCP和PP還沒有完全混合均勻就大量分解,短時間內產生大量PP自由基,導致 PP部分交聯,形成局部高強度熔體,熔體強度的不均勻性導致發泡不均勻,形成凹凸不平的表面。以PP1/PP2質量比2/3共混物做基礎樹脂,選取 DBP/DCP質量比90/10,考察引發劑用量和發泡性能的關系,結果見圖1。1 引發劑含量與發泡性能關系由圖1可看出,隨引發劑含量增加,單位體積泡孔數量先增加后基本不變;而發泡材料表觀密度逐漸降低,因此總引發劑含量不宜低于0.15份。這是由于當引發劑含量低時,引發劑濃度不足,PP接枝率不高,熔體強度不足,難以包裹住氣體,泡孔較大,并有部分泡孔破裂,導致發泡片密度較高;隨引發劑含量增加,PP接枝程度提高,熔體強度相應增加,氣泡在膨脹過程中,泡壁不易破裂,形成致密均勻的泡孔,單位體積泡孔數量增加,材料密度下降;隨引發劑含量進一步提高,熔體強度高于氣泡膨脹的動力,使氣泡不能充分膨脹,導致發泡片密度略有提高。.2 發泡劑的選擇與用量圖2是發泡劑 AC含量與發泡材料表觀密度及其泡孔密度的關系。由看出,起初隨發泡劑AC含量的增加,發泡材料表觀密度降低,泡孔密度提高,這是由于發泡劑分解產生的氣體隨其用量增加而增加,部分未分解的發泡劑在熔體中也起了發泡成核劑的作用。但在發泡劑含量增加到0.5份時,發泡材料表觀密度反而回升,泡孔密度下降。這是由于隨發泡劑含量的進一步提高,熔體中氣體含量過多,氣泡膨脹加劇,導致部分泡孔破裂合并,氣體溢出,于是發泡材料表觀密度又提高,泡孔密度下降。由還可看出,發泡劑的合適用量為0.3~0.5份。

安徽聚乳酸發泡材料定制
與傳統注塑制品相比,微孔發泡注塑制品具有質量更輕、翹曲和內部殘余應力更少、尺寸穩定性好、成型周期短等一系列優點。目前,欠注發泡成型是微孔注塑技術中應用為廣泛的工藝之一,具有操作簡單、效率高、能夠生產復雜制件,且能耗少,符合節約材料,降低成本這一發展理念,滿足發泡產品市場化的需求。然而,欠注發泡成型工藝也存在發泡制品內部泡孔易發生大量變形,泡孔尺寸分布不均勻,所得制品表面存在大量的氣痕、銀紋等缺陷,制約了其力學性能的提高和外觀視覺,阻礙了欠注發泡制品的進一步應用。家復合改性聚合物材料工程技術研究中心的何力團隊采用自主研發的氣體反壓裝置,利用化學欠注發泡工藝研究氣體反壓(GCP)對微孔注塑過程中發泡行為的影響。研究發現,采用氣體反壓可以減少發泡注塑制品的泡孔變形以及不均勻等缺點,改善了泡孔的形態。丙烯微孔發泡實驗方法將PP、發泡劑(AC)、發泡助劑[Zn(St)2/ZnO]按照98.5∶1∶0.5的比例混合均勻后加入料筒中進行塑化。然后打開氣體反壓裝置,在型腔中分別注入固定的GCP為0,0.2,0.4,0.6,0.8?MPa的氣體,隨后按照表1的工藝參數注射熔融樹脂進行發泡,冷卻后,取出PP發泡樣品。GCP對充模過程中熔體壓力的影響熔體注射完后,熔體壓力瞬間達到大值。隨著GCP從0增加至0.8?MPa,熔體內部大壓力從1.55?MPa增大到2.16?MPa,注射完成后,隨著氣體的排出,熔體壓力瞬間下降,隨著冷卻收縮,熔體壓力逐漸趨于0?MPa。由此可知,GCP可以明顯地提高熔體充模過程中的熔體壓力,改善欠注發泡過程中的熔體壓力環境。CP對泡孔質量的影響在沒有施加氣體反壓時,由于熔體流動速率遠大于泡孔的膨脹速率,泡孔發生流動剪切變形,導致末端位置的泡孔在皮層區域受到剪切作用時間和作用力較大,在流動方向上出現很大的變形,泡孔發生撕裂合并現象,泡孔形貌極不規則,而中間區域的泡孔形態受到剪切力較小,呈現規整圓形形態。同時發現,隨著GCP的增大,皮層附近撕裂變形的泡孔區域變小,熔體內部芯層泡孔從橢圓形向規整圓形形態轉變,規則泡孔區域所占比例增大,泡孔之間呈現獨立分布。當GCP達到0.8?MPa時,皮層附近泡孔呈現出相對較好的圓形形態,此時整體泡孔的變形較小。是因為GCP可以有效地降低泡孔在充模過程中受到的流動剪切作用,GCP值越大,泡孔在遷移過程中受到熔體壓力越大,泡孔受到熔體的約束力大,泡孔不易發生變形。GCP對結構參數的影響CP對泡孔結構參數的影響如下圖所示。可知,在常壓下泡孔的非變形層(也就是規則泡孔區)厚度僅占整個樣品厚度的10.9%;隨著GCP的增大,泡孔的非變形層所占比例逐漸升高,GCP為0.8 MPa時,升高至26.7%。而泡孔變形層區域厚度所占比例隨著GCP的增大而大幅度下降,從63.7%下降到45.4%,這說明GCP可以減小泡孔變形層,增大規則泡孔區域范圍。對變形層的泡孔變形度進行統計,如下圖所示,泡孔的平均長度隨著GCP的增加,整體呈現減小的趨勢,泡孔的平均寬度隨著GCP的增加而逐漸增大,泡孔的變形度隨GCP的增大而減小,由常壓下0.530的泡孔變形度降低到GCP為0.8?MPa下的0.304泡孔變形度,即GCP可以減小泡孔長度與寬度的差距,使變形區的泡孔變形程度減小。對不同GCP下泡孔非變形層的泡孔直徑進行統計,見圖c,隨著GCP的增加,當GCP為0.2?MPa時泡孔直徑略有減小,但隨著GCP的進一步增大,泡孔直徑從36.09?μm增大到41.93?μm。這是因為GCP的增大使得熔體的壓力也隨之增大,使得泡孔的成核臨界能壘升高,泡孔的成核速率下降,泡孔在充模過程中受到流動場的影響減弱,更多的氣體在卸壓階段促進泡孔的生長,因此熔體壓力越大,泡孔直徑越大。

安徽聚乳酸發泡材料定制
當熱塑性聚氨酯聚合物在1950年代問世時,TPE成為商業現實。在1960年代,苯乙烯嵌段共聚物問世,在1970年代,各種TPE出現。TPE的全球使用量(1990年為680000噸/年)以每年約9%的速度增長。由于聚苯乙烯和聚丁二烯之間的不相容性,苯乙烯-丁二烯材料具有兩相微觀結構塊,前者根據確切的成分分成球體或棒。由于聚苯乙烯含量低,該材料具有彈性,聚丁二烯的特性占主導地位。通常,它們提供比傳統交聯橡膠更廣泛的性能,因為其成分可以變化以適應最終的構造目標。嵌段共聚物很有趣,因為它們可以“微相分離”以形成周期性納米結構,苯乙烯-丁二烯-苯乙烯(SBS)嵌段共聚物。這種聚合物被稱為Kraton,用于鞋底和粘合劑。由于微細結構,需要透射電子顯微鏡(TEM)來檢查結構。丁二烯基質用四氧化鋨染色以在圖像中提供對比度。該材料是通過活性聚合制成的,因此塊體幾乎是單分散的,因此有助于形成非常規則的微觀結構。由于大多數聚合物彼此不相容,形成嵌段聚合物通常會導致相分離,并且自從引入SBS嵌段聚合物以來,該原理已被廣泛采用,特別是在其中一種嵌段是高度結晶的情況下。不相容規則的一個例外是Noryl材料,其中聚苯乙烯和聚苯醚或PPO相互形成連續共混物。其他TPE具有結晶域,其中一種嵌段與相鄰鏈中的其他嵌段共結晶,例如在共聚酯橡膠中,實現與SBS嵌段聚合物相同的效果。取決于嵌段長度,由于較高的晶體熔點,域通常比后者更穩定。該點決定了材料成型所需的加工溫度,以及產品的最終使用溫度。這樣的材料包括Hytrel,一種聚酯-聚醚共聚物和Pebax,一種尼龍或聚酰胺-聚醚共聚物。熱塑性彈性體(TPE),有時也稱為熱塑性橡膠,是一類共聚物或聚合物(通常是塑料和橡膠)的物理混合物,由具有熱塑性和彈性體特性的材料組成。雖然大多數彈性體是熱固性塑料,但相比之下,熱塑性塑料在制造中相對容易使用,例如通過注塑成型。熱塑性彈性體顯示出橡膠材料和塑料材料的典型優勢。使用熱塑性彈性體的好處是能夠拉伸到適度的伸長率并恢復到接近原始形狀的能力,從而比其他材料具有更長的使用壽命和更好的物理范圍。熱固性彈性體和熱塑性彈性體之間的主要區別在于其結構中的交聯鍵類型。事實上,交聯是賦予高彈性性能的關鍵結構因素。類型商業TPE有六類通用類別(名稱符合ISO18064):苯乙烯嵌段共聚物,TPS(TPE-s);熱塑性聚烯烴彈性體;熱塑性硫化橡膠,TPV(TPE-v或TPV);熱塑性聚氨酯,TPU(TPU);熱塑性共聚酯,TPC(TPE-E);熱塑性聚酰胺,TPA(TPE-A);未分類的熱塑性彈性體,TPZ。來自嵌段共聚物組的TPE材料的例子包括CAWITON、THERMOLASTK、THERMOLASTM、Arnitel、Hytrel、Dryflex、Mediprene、Kraton、Pibiflex、Sofprene和Laprene。這些苯乙烯嵌段共聚物(TPE-s)中有CAWITON、THERMOLASTK、THERMOLASTM、Sofprene、Dryflex和Laprene。Laripur、Desmopan或Elastollan是熱塑性聚氨酯(TPU)的例子。Sarlink、Santoprene、Termoton、Solprene、THERMOLASTV、Vegaprene、或Forprene是TPV材料的例子。熱塑性烯烴彈性體(TPO)化合物的例子是For-TecE或Engage。Ninjaflex用于3D打印。為了符合熱塑性彈性體的資格,材料必須具有以下三個基本特征:1.拉伸到適度伸長的能力。2.并在消除應力后恢復到接近其原始形狀的狀態.3.可在高溫下作為熔體加工,沒有明顯的蠕變。TPE用于傳統彈性體無法提供產品所需物理性能范圍的地方。這些材料在汽車領域和家用電器領域有大量應用。2014年,TPE的全球市場規模達到約167億美元。大約40%的TPE產品用于汽車制造。例如,共聚酯TPE用于雪地摩托軌道,其中剛度和耐磨性非常重要。熱塑性烯烴(TPO)越來越多地用作屋頂材料。TPE也廣泛用于導管尼龍嵌段共聚物為患者提供了一系列理想的柔軟度。熱塑性有機硅和烯烴混合物用于擠出玻璃滑道和動態擋風雨條汽車型材。苯乙烯嵌段共聚物因其易于加工而用于鞋底,并廣泛用作粘合劑。 由于在對各種熱塑性基材進行雙組分注塑成型方面具有無與倫比的能力,工程TPS材料還涵蓋了從汽車市場到消費品和醫療產品的廣泛技術應用。例如,柔軟的抓握表面、設計元素、背光開關和表面,以及密封件、墊圈或阻尼元件。TPE通常用于制造汽車性能應用的懸架襯套,因為與常規橡膠襯套相比,它具有更大的抗變形能力。由于改性塑料樹脂的功能、成本效益和適應性,熱塑性塑料在供暖、通風和空調(HVAC)行業經歷了增長成各種蓋子、風扇和外殼。TPE還可用于醫療設備、電纜護套和內絕緣、性玩具和一些耳機電纜。 不僅用于工業用途,還用于運動鞋和背包等消費品。您可以在許多運動和戶外品牌產品中看到基于TPE的材料“ARIAPRENE”。2021年,全新的TPE回收理念問世,稱為APTERRA,它是GRS(全球回收標準)收集和再生泡沫織物廠廢料,因為每次生產運行總是有20%的廢料。

安徽聚乳酸發泡材料定制
近年來綜合性能優異、可回收易降解的聚丙烯發泡材料已成為泡沫塑料家族中的“新寵”,是聚合物泡沫材料中增長速度快的品種。超臨界二氧化碳(CO2)發泡聚合物技術是制備聚丙烯微孔發泡材料的關鍵核心技術,近日華東理工大學化工學院趙玲教授團隊在該技術領域取得了實質性突破,成功開發了高性能聚丙烯微孔發泡材料綠色制備過程的優化和強化技術。聚合物發泡有物理發泡劑和化學發泡劑兩大類。化學發泡劑存在化學殘留、發泡過程難控制和不易獲得高發泡倍率等缺點;物理發泡劑中的氟氯烴類則對臭氧層有破壞作用,已逐漸被禁止和限制使用;而一些新型氟碳氫化合物的全球變暖潛能值仍相對較高,烷烴類發泡劑則易燃燒不安全。相比這些傳統的發泡劑,超臨界CO2發泡聚合物技術作為綠色制造技術,已被工信部列入我國優先發展的產業關鍵共性技術,而且CO2進入聚合物后會引起熔點、表面張力和黏度下降、結晶行為改變等一系列變化,可以制備微孔甚至納米泡孔材料。聚丙烯微孔發泡聚丙烯是結晶聚合物,低溫固態發泡受結晶限制,很難制備高發泡倍率產品;高溫發泡聚合物熔體強度不夠無法保持完整泡孔,可操作窗口窄。因此,大規模制造具有穩定均勻泡孔形貌和外形尺寸的高發泡倍率微孔材料難度大。為了攻克這一難題,趙玲團隊聯合無錫會通、中石化北化院、浙江新恒泰、鎮海煉化等單位,在合適物料體系、可控工藝過程和高效工業裝備等方面開展了超臨界CO2發泡聚丙烯的優化、強化和工程化等系列工作,形成了“適合超臨界CO2發泡的聚丙烯專用料”“分步/分段發泡新工藝”“優化構建流場結構實現高效規模制備”三大技術創新。趙玲介紹,在低于流動溫度的可變形區發泡,既可突破結晶的制約,又能保證發泡材料微孔結構和外形尺寸穩定成型。基于這一發泡機制,他們開發了兼具較寬發泡溫度窗口和較強的CO2溶解擴散能力的聚丙烯發泡專用料,以及能改善泡孔結構和表觀形態的新型功能助劑/添加劑。CO2變壓飽和提高了過程效率和發泡倍率,氣泡成核和生長的分段實施減小了高壓設備體積;同時釜壓發泡、模壓發泡等高壓設備和聚合物預成型體的結構優化設計,保證了均勻的壓力場、溫度場和速度場,實現了低密度聚丙烯微孔發泡材料的規模制造和柔性生產。利用上述創新技術,項目團隊建設了2套年產3萬立方米模壓發泡裝置,實現了低密度聚丙烯微孔厚板的制造;新建了4套、優化改造了3套年產4萬~6萬立方米的釜壓發泡裝置,生產效率提高25%,成品率提高到99%以上,發泡專用料已在鎮海煉化生產,2016~2018年新增產值3.31億元、利稅1.09億元。此外,該團隊已獲得授權發明專利8件、實用新型專利8件;相關研究成果發表了46篇SCI/EI收錄論文
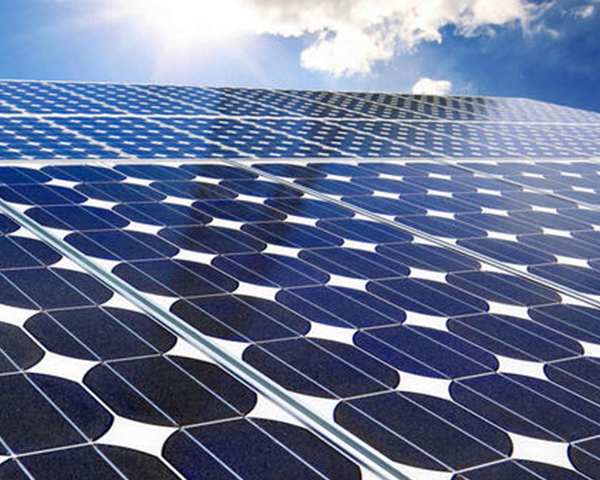
安徽聚乳酸發泡材料定制
簡述聚丙烯微孔發泡新材料(Microcellular Polypropylene foam), 簡稱MPP,是特指泡孔尺寸小于100微米的聚丙烯多孔發泡材料(更嚴格地定義是泡孔尺寸小于10微米,泡孔密度大于10的9次方個/cm3)。由于材料內部大量微米級泡孔的存在,MPP具有優異的減震、緩沖、隔熱和吸聲等性能,可廣泛應用于包裝、交通工具、箱包、體育器材等領域,是傳統EVA、PU、PS發泡材料、EPE和EPP的替代物。聚丙烯微孔發泡性能與應用應用超臨界二氧化碳技術(supercritical carbon dioxide) 制備MPP,在高溫高壓下將二氧化碳氣體導入聚丙烯材料基體,并誘導其成核、發泡,形成含有大量微米尺度泡孔的微孔發泡材料。發泡過程清潔無污染,發泡制品衛生環保。發泡過程PP材料未發生交聯,因此可回收循環使用。丙烯(PP)本身是無毒材料,是目前嬰兒奶瓶和可微波加熱餐盒的常用材料。清潔衛生的MPP特別適合于醫療器械、食品等包裝材料衛生等級要求較高的領域。也可應用于兒童拼圖、玩具等對產品健康要求較高的領域,代替常用的由AC發泡劑制造的交聯PE泡沫,EVA泡沫。PP是半結晶聚合物,其熔點一般150~170℃。相比于耐溫只有70~80℃的PE、PS、PU發泡材料,MPP的使用溫度可達120℃,因此MPP特別適合高溫包裝、高溫保溫等領域。MPP集增強、隔熱和降噪為一體,也特別適用于對材料輕量化要求較高的領域,如汽車、軌道交通,船舶,風機葉片等。輕質高強的MPP厚板作為結構泡沫使用,代替傳統的結構泡沫如PVC/PU互穿結構泡沫、PET結構泡沫等,特別是作為三明治夾芯復合材料的芯材使用。MPP微米尺度的泡孔賦予材料的特別之處有:(1) 同等發泡倍率(或表觀密度)下,由于泡孔較小,微孔發泡材料的機械性能損失較小。這意味著使用MPP可以更加節約材料,更加降低制品重量和體積。2) 由于泡孔尺寸在1-100μm之間可控,MPP可以被剖切成厚度小于0.1mm的超薄片材,而片材表面不會穿孔,可應用于微電子器件的包裝。(3) 由于表面大量微米級泡孔的存在,MPP適合作為液晶顯示器背光模組的反射板,提高漫反射率。(4) 微米尺度的泡孔有效降低了泡孔內氣體的對流,從而有效降低了由空氣對流引起的熱傳遞。因此高倍率的微孔發泡材料具有較低的、依賴于泡孔結構的長期穩定的低導熱系數。(5) 輕質高強的MPP片材適合于作為揚聲器振膜使用。(6) 同樣由于其微米尺度的泡孔,MPP具有極佳的表面保護性能,可應用于液晶面板等防護性要求較高的包裝領域。