成都可降解包裝材料價格
發布時間:2024-11-07 00:57:57
成都可降解包裝材料價格
生物降解塑料目前已開始應用在一次性餐具、包裝、農業、汽車、醫療、紡織等多個領域,基于行業發展趨勢及市場需求,第八元素為客戶提供PLA、PBAT、PBS等降解材料,點擊以下鏈接,即可在線采購樣品:系統介紹車用聚丙烯的類型,應用方向,性能要求。用PP丙烯微孔發泡隨著汽車工業的蓬勃發展,制造汽車的各種原材料也迅速發展和更新換代,越來越多的汽車零部件開始采用改性塑料替代金屬制件。塑料在汽車上的應用已有近50年的歷史,目前汽車用改性塑料的使用量已成為衡量汽車設計和制造水平高低的一個重要標志,塑料飾件的大量應用,促進了汽車的減重節能,提高了汽車的美觀舒適度。PP以密度小、性價比高、具有優異的耐熱性能、耐化學藥品腐蝕性、剛性、易于成型加工和回收利用等特性在汽車上得到了廣泛的應用。近來更是有把汽車內飾和外裝材料統一到PP系列材料的趨勢。由于高性能基礎樹脂的開發生產周期長、投資巨大、技術要求高,且需要高精尖的集成先進綜合技術,所以對現有PP樹脂需要進行更廣泛、更有效、更經濟、更實用的改性。延伸性、機械的強度和抗斷裂性無機填料和彈性體增韌增強改性PP主要是“三高”。是由 PP樹脂、三元乙丙橡膠(EPDM)和乙烯-辛烯共聚物(POE)等增韌彈性體及滑石粉、碳酸鈣等無機填料的復合物,其主要用于汽車保險杠的注射成型,且改性PP保險杠具有成本低、質輕、易涂裝、可循環使用等優點。滑石粉填充改性PP材料具有高剛性、低熱膨脹系數和低收縮率,且其抗化學腐蝕性能強,尤其是經表面處理的滑石粉填充PP可有效改善PP的沖擊性能,提高材料的模量和熱變形溫度。玻璃纖維增強改性PP玻璃纖維增強改性PP材料尤其是LGFPP材料在汽車部件上的研究與應用(如在前端模塊、儀表板骨架、車門模塊等典型部件的應用)是多年來的研究熱點之一。LGFPP制品指含有長度為10~25mm的玻璃纖維改性的PP復合材料經過注塑等工藝形成的三維結構。10~25mm的長玻璃纖維增強聚合物相比普通4~7mm的短玻璃纖維增強聚合物具有更高的強度、剛度、韌性,以及尺寸穩定性好、翹曲度低等優勢。此外,LGFPP材料比短玻璃纖維增強PP(GFPP)有著更好的抗蠕變性能,即使經受100℃的高溫也不會產生明顯的蠕變。與金屬材料和熱固性復合材料相比,LG-FPP的密度低,相同部件的質量可減輕20%~50%;LGFPP能為設計人員提供更大的設計靈活性,可成型形狀復雜的部件、提高集成汽車零部件的能力、節約模具成本(一般長玻璃纖維增強聚合物注塑模具的成本約為金屬沖壓模具成本的20%)、減少能耗(長玻璃纖維增強聚合物的生產能耗僅為鋼制品的60%~80%,鋁制品的35%~50%)、簡化裝配工序。汽車部件用礦物纖維增強PP的新產品,具有強度高、熱膨脹系數低、耐高溫、阻燃性能好、低浮纖、低翹曲、低收縮 等特點。
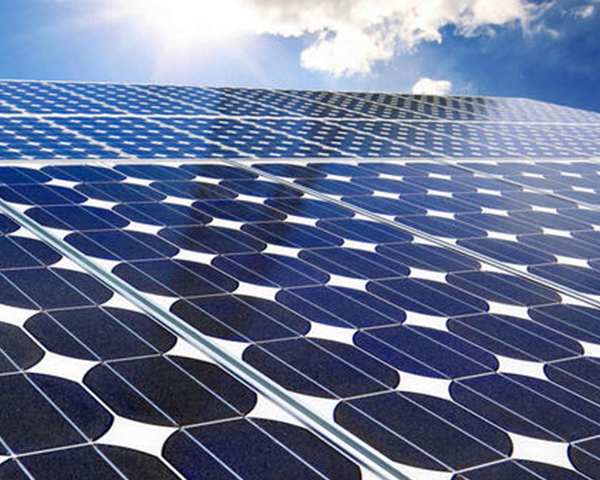
成都可降解包裝材料價格
年來綜合性能優異、可回收易降解的聚丙烯發泡材料已成為泡沫塑料家族中的“新寵”,是聚合物泡沫材料中增長速度快的品種。超臨界二氧化碳(CO2)發泡聚合物技術是制備聚丙烯微孔發泡材料的關鍵核心技術,近日華東理工大學化工學院趙玲教授團隊在該技術領域取得了實質性突破,成功開發了高性能聚丙烯微孔發泡材料綠色制備過程的優化和強化技術。聚合物發泡有物理發泡劑和化學發泡劑兩大類。化學發泡劑存在化學殘留、發泡過程難控制和不易獲得高發泡倍率等缺點;物理發泡劑中的氟氯烴類則對臭氧層有破壞作用,已逐漸被禁止和限制使用;而一些新型氟碳氫化合物的全球變暖潛能值仍相對較高,烷烴類發泡劑則易燃燒不安全。相比這些傳統的發泡劑,超臨界CO2發泡聚合物技術作為綠色制造技術,已被工信部列入我國優先發展的產業關鍵共性技術,而且CO2進入聚合物后會引起熔點、表面張力和黏度下降、結晶行為改變等一系列變化,可以制備微孔甚至納米泡孔材料。丙烯微孔發泡丙烯是結晶聚合物,低溫固態發泡受結晶限制,很難制備高發泡倍率產品;高溫發泡聚合物熔體強度不夠無法保持完整泡孔,可操作窗口窄。因,大規模制造具有穩定均勻泡孔形貌和外形尺寸的高發泡倍率微孔材料難度大。為了攻克這一難題,趙玲團隊聯合無錫會通、中石化北化院、浙江新恒泰、鎮海煉化等單位,在合適物料體系、可控工藝過程和高效工業裝備等方面開展了超臨界CO2發泡聚丙烯的優化、強化和工程化等系列工作,形成了“適合超臨界CO2發泡的聚丙烯專用料”“分步/分段發泡新工藝”“優化構建流場結構實現高效規模制備”三大技術創新。趙玲介紹,在低于流動溫度的可變形區發泡,既可突破結晶的制約,又能保證發泡材料微孔結構和外形尺寸穩定成型。基于這一發泡機制,他們開發了兼具較寬發泡溫度窗口和較強的CO2溶解擴散能力的聚丙烯發泡專用料,以及能改善泡孔結構和表觀形態的新型功能助劑/添加劑。CO2變壓飽和提高了過程效率和發泡倍率,氣泡成核和生長的分段實施減小了高壓設備體積;同時釜壓發泡、模壓發泡等高壓設備和聚合物預成型體的結構優化設計,保證了均勻的壓力場、溫度場和速度場,實現了低密度聚丙烯微孔發泡材料的規模制造和柔性生產。利用上述創新技術,項目團隊建設了2套年產3萬立方米模壓發泡裝置,實現了低密度聚丙烯微孔厚板的制造;新建了4套、優化改造了3套年產4萬~6萬立方米的釜壓發泡裝置,生產效率提高25%,成品率提高到99%以上,發泡專用料已在鎮海煉化生產,2016~2018年新增產值3.31億元、利稅1.09億元。此外,該團隊已獲得授權發明專利8件、實用新型專利8件;相關研究成果發表了46篇SCI/EI收錄論文。趙玲表示,超臨界CO2模壓發泡技術通用性強,除聚丙烯外,還可用于聚氨酯彈性體微孔發泡材料的生產,多種熱塑性聚合物及其復合材料的中試已經完成。采用該技術生產的聚丙烯發泡專用料,除可應用于汽車零部件和內飾、緩沖包裝等傳統領域,還可滿足兒童玩具、食品、醫療、家居用品等領域對綠色材料的需求。由于微孔賦予了聚丙烯獨特的性能,聚丙烯微孔發泡材料還可應用于更多的新興領域,如新能源汽車動力電池墊片、5G通信微波中繼天線罩、高檔汽車音響振膜、防彈衣背板等。

成都可降解包裝材料價格
微發泡注塑,聚丙烯/橡膠/滑石粉復合材料,增強增韌聚丙烯微孔發泡聚丙烯作為一種經濟高效的熱塑性聚合物,具有材料成本低、抗腐蝕性好、比強度高和易于成型加工等優點,已廣泛應用于包裝工程、紡織、電子產品以及汽車工業。以汽車工業為例,聚丙烯的年均用量高達255.6百萬噸,研究表明汽車每減重10%就可以將燃料的利用率提高至少6%。因此,近年來為了節省材料和能源、減少環境污染進而實現經濟社會的健康可持續發展,塑料制品的輕量化問題引起了廣大學者的研究興趣,而其中發泡注塑成型工藝被視為是一種非常有前途的輕量化實現方式。然而,由于聚丙烯的熔體強度低,導致其發泡能力非常差,常規微發泡注塑聚丙烯產品存在泡孔尺寸大且分布極其不均勻,嚴重降低了其力學性能,尤其是沖擊力學性能。針對上述問題,山東大學材料科學與工程學院王桂龍和合作者提出了一種利用橡膠和滑石粉的耦合作用改性聚丙烯的新途徑,顯著提高了聚丙烯熔體強度和促進了結晶,進而改善了聚丙烯的發泡能力,終通過微發泡注塑制備了具有優異綜合力學性能的微孔聚丙烯制品。

成都可降解包裝材料價格
隨著國內大煉化項目、PDH項目陸續上馬,國內聚丙烯(PP)市場成為群雄角力之地。新建項目投產,PP產能仍將快速增長,預計到2023年我國PP產能將超過3500萬噸,自給率將近90%。屆時,高性能產品將成為企業突出重圍的殺手锏。高性能PP成投資熱土2020年已經有三家企業成功投產聚丙烯裝置,浙江石化、恒力石化、利和知信。近一個月,聚烯烴行業掀起了新一波高性能PP投資熱潮:4月22日,總投資約100億美元的埃克森美孚廣東惠州乙烯項目正式動工,項目包括乙烯裝置和高端PE、PP等生產裝置,采用已經成功應用、先進的專有工藝和催化劑技術生產高性能聚合物。聚丙烯微孔發泡5月17日,總投資約56億美元的中海殼牌惠州三期乙烯項目合作框架協議簽約,項目產品包括聚α烯烴、高碳合成醇、茂金屬PE、共聚PP等,共14規模生產裝置。18日,徐州海天石化集團年產10萬噸高性能PP樹脂項目“云簽約”,落戶大慶龍鳳區。高性能產品研發能力不足我國已投入生產的高端聚丙烯專用樹脂有:三元共聚聚丙烯薄膜專用料F5606、管材專用料、薄壁注塑料M50T、高熔體強度薄膜專用料、丙丁共聚膜料、低溫抗沖注塑專用料、氫調法高流動注塑料、高透明注塑專用料、抗菌系列專用料、低灰分PP、快速成型PP、透明PP專用料等。但由于我國高端聚丙烯產品研發能力不足,且同質化嚴重,一些高性能和特殊性能產品,如茂金屬PP(mPP)、特種雙向拉伸聚丙烯(BOPP)膜、流延聚丙烯(CPP)膜等仍需大量進口來滿足國內市場需求。我國mPP年消費量約10萬噸,除燕山石化少量供應市場,基本依賴進口,主要用于生產醫用或食品用高透明PP制品、食品包裝薄膜、無紡布、超細旦丙綸纖維等領域。具有高拉伸速度與幅寬、超薄、超透及更好低溫熱封性能的特種BOPP薄膜、電工膜、電容器膜、鍍鋁膜等PP薄膜料以及汽車和家電用PP注塑料的年進口量均超百萬噸。PP管材料的年進口量約50萬噸。高性能PP開發方向1抗菌PP此次新冠肺炎疫情的肆虐,推動汽車生產商聚焦抗菌PP在內飾件中的應用,這或將成為車用PP下一個熱點應用領域。2玻纖增強PP長玻纖增強PP材料因具備更高的強度、剛度、韌度、尺寸穩定性,廣泛應用于儀表骨架板、車門組合件、前端組件、車身門板模塊、車頂面板、座椅骨架等汽車部件上。長玻纖增強PP材料在120℃時的高溫疲勞強度是普通玻纖增強PP材料的2倍,甚至比以耐熱性著稱的玻纖增強尼龍材料高10%,具有作為結構件所需的耐久性和可靠性。氣味散發耐刮擦PP隨著人們對汽車品質的追求,車用PP材料需要滿足的已不僅僅是力學性能,還有對外觀、環保等方面的高要求。目前市場上低氣味散發PP材料多被Basell、北歐化工等公司產品壟斷,國產替代進口任務艱巨。制造高抗刮擦汽車內飾件材料一方面要采用國外表面硬度較高的PP原料,另一方面需要添加助劑提升材料表面的爽滑度。但助劑在體系內受熱會有小分子散發影響車內空氣質量,同時又會出現表面遷移現象,影響內飾件外觀。因此,問題核心仍取決于PP基材的性能。

成都可降解包裝材料價格
聚丙烯微孔發泡材料的特殊應用價值:微孔發泡材料的韌性高、疲勞壽命長、比強度高、熱穩定性高、介電常數低。除此之外還有質輕、隔熱、吸震、隔音、價格低廉等特點。這是因為這種材料中有比塑料中原有的缺陷或微細裂縫小得多的孔徑,這種孔徑能鈍化塑料中原有裂縫的尖端,所以不會降低塑料的強度。因此,在汽車、航天航空和其他各種運輸工具等領域有特殊的應用價值。聚丙烯微孔發泡通過研究熔體流動速率和微孔發泡PP性能之間的關系發現,低熔體流動速率的聚丙烯微孔發泡材料具有良好的機械性能。日本Sumitom化學公司利用幾種熔體流動速率不同的聚合物共混發泡,制得了一種沖擊強度高且具有類似于皮革結構紋理的柔軟片材,這種泡沫塑料的發泡倍率在1.1~2.0之間。聚丙烯微孔發泡材料成核劑改性聚丙烯材料:PP是一種不完全結晶的通用塑料,它的結晶速度較慢慢,容易形成尺寸較大的球晶,導致制品的光澤度和透明性差,制品的外觀缺乏美感,限制了其在透明包裝和日用品等領域的應用。利用成核劑改性聚丙烯,是一種制備透明度高,力學性能優異的聚丙烯材料的簡單有效的方法,因此在聚丙烯的改性當中被廣泛應用。陳枝晴等研究了聚丙烯的透明性,適量的成核劑和相應的分散劑能提高聚丙烯的透明性;且共聚PP的透明性比均聚PP好。張廣平等采用2,2-亞甲基-雙(4,6-二叔丁基苯基)磷酸及其衍生物作為聚丙烯的成核劑,研究了成核劑對復合材料力學性能的影響。結果表明:這種成核劑的佳質量分數為0.4%。此時,復合材料的結晶溫度提高了11℃~15℃,結晶度增加3%~6%,結晶速率顯著增加;材料的模量提高了20%~30%,彎曲強度也提高了10%~20%。纖維增強聚丙烯材料:纖維增強聚丙烯復合材料是目前熱塑性塑料市場中增長較快的塑料品種之一,尤其是在汽車用塑料中。為了能夠更好的發揮纖維的增強作用,在塑料中纖維長度需要大于LC,既零界長度,LC取值與塑料的種類有直接關系。如果纖維的長度小于LC,其增強效果與一般的粉末填料區別不大。例如,玻纖增強PP中,玻璃纖維的零界長度為3.1 mm;而在另外一種經過化學改性的PP中,LC可能降到0.9mm以下。對于普通的短玻纖增強塑料,制品中的纖維長度一般只有0.2~0.6mm,限制了制成品性能的提高。而在長玻纖增強塑料部件中,玻璃纖維的殘留長度可以達到3mm以上,大大提高了制品的物理機械性能。聚丙烯微孔發泡材料應用價值由于長纖維增強熱塑性塑料制品中的纖維殘留長度較長,它的沖擊強度比普通的纖維增強材料高了4倍左右;比強度(17.2%)更是比鋁材料(9.8%)都高;此外,這種材料的加工流動性好,制品外觀光亮、無塌坑等缺陷,制品的成型收縮率也小。的研究成果表明,長玻纖增強聚丙烯(LFG/PP)和短玻纖增強聚丙烯(SFG/PP)的玻璃纖維直徑和含量相同時,LFG/PP的拉伸強度、彎曲強度和沖擊強度明顯高于SFG/PP。

成都可降解包裝材料價格
隨著汽車工業的蓬勃發展,制造汽車的各種原材料也迅速發展和更新換代,越來越多的汽車零部件開始采用改性塑料替代金屬制件。塑料在汽車上的應用已有近50年的歷史,目前汽車用改性塑料的使用量已成為衡量汽車設計和制造水平高低的一個重要標志,塑料飾件的大量應用,促進了汽車的減重節能,提高了汽車的美觀舒適度。P以密度小、性價比高、具有優異的耐熱性能、耐化學藥品腐蝕性、剛性、易于成型加工和回收利用等特性在汽車上得到了廣泛的應用。近來更是有把汽車內飾和外裝材料統一到PP系列材料的趨勢。由于高性能基礎樹脂的開發生產周期長、投資巨大、技術要求高,且需要高精尖的集成先進綜合技術,所以對現有PP樹脂需要進行更廣泛、更有效、更經濟、更實用的改性。聚丙烯微孔發泡微發泡(Microcellular Foaming)是指以熱塑性材料為基體,制品中間層密布尺寸從十到幾十微米的封閉微孔。微發泡注塑成型技術突破了傳統注塑的諸多局限,在基本保證制品性能的基礎上,可以明顯減輕重量和成型的周期,大大降低機臺的鎖模力,并具有內應力和翹曲小、平直度高,沒有縮水,尺寸穩定,成型視窗大等特點,特別是在生產高精密和材料較貴的制品上與常規注塑相比較獨具優勢,成為近年來注塑技術發展的一個重要方向。聚丙烯微發泡材料能夠滿足大型微發泡汽車注塑件。隨著汽車輕量化的發展,選用PP發泡材料已成為汽車減重的重要途徑,目前其在汽車內飾上的應用也越來越多,其中PP發泡材料在各種汽車上的使用占比為轎車占45%,卡車、工程機械車占20% ,客車、商務車占35% 。汽車用PP發泡材料主要為化學微發泡材料。普通微發泡PP制品的表觀質量很不理想,僅適合于需要表面覆皮的高端車,不僅增加了制造成本,也限制了PP發泡材料的推廣和應用;而化學微孔發泡是以熱塑性材料為基體,化學發泡劑為氣源,通過自鎖工藝使得氣體形成超臨界狀態,注入模腔后氣體在擴散內壓的作用下,使制品中間分布著直徑從十幾到幾十微米的封閉微孔泡,且其理想的泡孔直徑應 <50μm ,但目前國內行業實際生產的微發泡PP的微泡孔直徑約為80~350μm 。對于微孔發泡主要有注塑微發泡、吹塑微發泡和擠出微發泡等,注塑微發泡適用于各種汽車內外飾件,如車身門板、尾門、風道等;擠出微發泡適用于密封條、頂棚等;吹塑微發泡適用于汽車風管等。利用微發泡技術可使PP制品的質量減少約10%~20% ,較傳統材料在部件上可實現高50%的減重,注射壓力降低約30%~50% ,鎖模力降低約20% ,循環周期減少10%~15%,同時還能提高汽車的節能性,較傳統材料可實現高30%的節能,并且能改善制品的翹曲變形性,使產品和模具的設計更靈活。輻射交聯PP高發泡片材具有良好的力學性能,作為汽車車頂,可降低汽車的質量,同時其還可用于汽車的內飾件,有利于汽車的輕量化。