昆山PLA發泡定制
發布時間:2024-08-22 01:02:33
昆山PLA發泡定制
微發泡注塑,聚丙烯/橡膠/滑石粉復合材料,增強增韌聚丙烯微孔發泡聚丙烯作為一種經濟高效的熱塑性聚合物,具有材料成本低、抗腐蝕性好、比強度高和易于成型加工等優點,已廣泛應用于包裝工程、紡織、電子產品以及汽車工業。以汽車工業為例,聚丙烯的年均用量高達255.6百萬噸,研究表明汽車每減重10%就可以將燃料的利用率提高至少6%。因此,近年來為了節省材料和能源、減少環境污染進而實現經濟社會的健康可持續發展,塑料制品的輕量化問題引起了廣大學者的研究興趣,而其中發泡注塑成型工藝被視為是一種非常有前途的輕量化實現方式。然而,由于聚丙烯的熔體強度低,導致其發泡能力非常差,常規微發泡注塑聚丙烯產品存在泡孔尺寸大且分布極其不均勻,嚴重降低了其力學性能,尤其是沖擊力學性能。針對上述問題,山東大學材料科學與工程學院王桂龍和合作者提出了一種利用橡膠和滑石粉的耦合作用改性聚丙烯的新途徑,顯著提高了聚丙烯熔體強度和促進了結晶,進而改善了聚丙烯的發泡能力,終通過微發泡注塑制備了具有優異綜合力學性能的微孔聚丙烯制品。
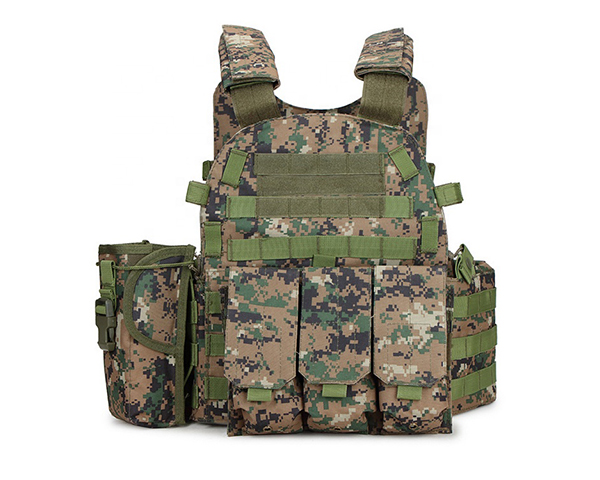
昆山PLA發泡定制
摘要:長玻纖增強聚丙烯材料(PP-LGF)作為一種輕質高強的復合材料,在滿足汽車零部件性能的同時,對零部件減重具有明顯貢獻,目前在汽車零部件應用上備受青睞。文章主要介紹了PP-LGF在汽車儀表板輕量化方面的應用和發展現狀,詳細介紹了薄壁注塑、物理發泡、化學發泡三種成型工藝實現儀表板輕量化的技術概況,并展望了PP-LGF在儀表板上的應用前景。聚丙烯微孔發泡近年來,隨著我國經濟的不斷發展,汽車工業也得到了快速發展。然而,由此引發的環境問題也日益嚴重,通過汽車輕量化來降低油耗從而降低環境污染,已經成為汽車行業的研究熱點,其中,使用質量更輕的非金屬材料替代傳統金屬材料的研究在近年來也取得了較大進展。運用復合材料來部分取代車身結構件及內、外飾裝飾件是汽車輕量化的一種行之有效的方法。在眾多的復合材料中,長玻纖增強聚丙烯材料(PP-LGF)以其低廉的價格、優良的力學性能和環境友好性而獲得更多的青睞。與短玻纖增強聚丙烯材料(PP-SGF)相比,PPLGF在強度、剛度、翹曲度、耐疲勞、缺口沖擊強度和尺寸穩定性等方面更具優勢,因此,使用PP-LGF生產的汽車零部件可進一步實現重量及成本的降低。1 長玻纖增強聚丙烯材料性能特點長玻纖增強聚丙烯材料的制備工藝主要分為5種,即熔融浸漬、溶液浸漬、粉末浸漬、纖維混編工藝以及薄膜疊層工藝,而在汽車零部件領域主要應用的為熔融浸漬法。熔融浸漬法生產的PP-LGF粒子的長度一般為8mm~15mm,其中玻纖的含量可達20%~60%,粒子中玻纖的保留長度可達1mm~3mm,如圖1所示,相較于玻纖保留長度僅為0.2mm~0.4mm的PP-SGF材料,PPLGF因其內部纖維構成的三維網絡結構,可保證產品具有更優的力學性能、抗沖擊性能、耐蠕變性能等特點,更加適合應用于汽車領域對結構性能要求較高的零部件。此外,隨著纖維含量的增加,PP-LGF的性能也隨之提高。長玻纖增強聚丙烯材料在儀表板上的應用儀表板是汽車內飾中的重要部件,為提升汽車內飾的感知質量,中、高檔車型普遍會采用軟質儀表板,即在儀表板骨架表面增加軟質表皮層。儀表板骨架作為儀表板系統的主體部件,同時也是電器件和其他功能件的承載結構,因此要求其具有高強度及高剛性,目前在儀表板骨架上使用為廣泛的為PP材料,采用相同密度的PP-LGF材料替代傳統PP材料,在滿足相關性能的同時,可提升儀表板吸能性能,同時可將現有儀表板骨架的設計厚度由3mm~3.5mm降低到1.8mm~2.5mm,從而降低儀表板骨架重量,推動汽車內飾輕量化。以下將從PP-LGF應用于儀表板上的薄壁注塑、物理發泡、化學發泡三種成型工藝方面,介紹PP-LGF在儀表板輕量化方面的應用。 2.1 薄壁注塑薄壁注塑工藝是直接將產品壁厚減薄,在模具中進行加工的一種成型方法,與傳統PP材料注塑的3mm~3.5mm壁厚的儀表板骨架相比,PP-LGF材料運用薄壁注塑工藝制造的儀表板骨架產品壁厚一般為2.5mm左右,整體減重可達約25%。該工藝的投入成本較低,重量優勢明顯。目前,該工藝在國內和國外合資品牌中,如吉利、大眾、上汽、福特等均有應用,一般選擇PPLGF20材料,設計的產品壁厚一般為2.2mm~2.5mm。然而,薄壁注塑工藝也存在兩點問題,首先是該工藝的模具成本較高,使用薄壁注塑,成型模具需要采用熱流道設計,熱流道模具的成本要比普通注塑工藝的模具成本高。其次,注塑工藝管控和注塑精度要求高,因為PP-LGF中長玻纖分布的各向異性,采用PP-LGF材料的薄壁注塑產品翹曲變形較為嚴重,尺寸穩定性較差。2.2 物理發泡物理發泡工藝又稱為MuCell 工藝,它是以熱塑性材料為基體,通過將超臨界流體(二氧化碳或氮氣) 溶解到熱熔膠中形成單相溶體,并保持在高壓力下,然后,通過開關式射嘴射進溫度和壓力較低的模具型腔,由于溫度和壓力降低引發分子的不穩定性從而在產品內部形成從十到幾十微米不等的封閉氣泡微孔[4-5],該項技術早期由麻省理工學院發明,1995年由美國Trexel公司將技術實現全球商品化。MuCell 工藝優勢為成型周期短、產品尺寸穩定性好、翹曲低、產品輕量化和工藝適用性廣。MuCell工藝使用超臨界流體,可有效降低PP-LGF材料黏度, 提高熔體流動性。泡孔成長壓力代替傳統注塑中的保壓階段,縮短成型周期,同時,可使壓力分布均勻,有效降低PPLGF產品內應力,降低因長玻纖各項異性導致的產品翹曲,增加產品的尺寸穩定性。另外,泡孔填充可有效避免產品表面縮痕,微孔結構擴充,降低材料密度,產品重量減輕,較同材質實體,重量可降低5%~10%。目前,福特新蒙迪歐在儀表板骨架上應用了該工藝,骨架產品設計壁厚2.4mm,相較于實心材料重量降低了10%,此外,長城和大眾也有應用于此項技術。MuCell 工藝的缺點是一次性投入高,工藝難度大,同時相關研究表明,使用該工藝對儀表板減重比控制在3%~8%時,產品性能會下降10%左右,基本滿足性能要求,減重超過8%,機械性能和耐熱老化性能急劇下降,不能滿足要求。若使用MuCell 工藝推薦減重比為3%~5%。2.3 化學發泡化學發泡工藝包括模內發泡工藝和二次開模發泡工藝(core-back),二者均是在注塑過程中,利用塑料粒子中加入的碳酸氫鈉和碳酸銨類的無機發泡劑,受熱分解產生的二氧化碳等氣體,使產品形成微孔發泡結構,以降低材料密度,減輕產品重量。其中,core-back工藝因使用了二次開模,相較于模內化學發泡,發泡的倍率更高,產品中形成的泡孔數量更多,產品的減重比更大。一般來說,模內化學發泡的減重比相比于實心材料在5%~8%左右,而core-back工藝可高達30%~50%,具體根據退模行程決定。同物理發泡工藝一樣,化學發泡工藝可在PP-LGF材料應用減重的同時,減少產品翹曲變形,提升產品穩定性,而且二次開模發泡工藝能夠適用于做外觀件。目前,寶馬5系已在儀表板骨架上應用了PP-LGF的core-back工藝,產品壁厚由初始1.8mm左右發泡到3.8mm,重量降低了約40%,此外大眾的部分車型也已使用模內化學發泡工藝。core-back工藝的缺點是發泡劑較貴,開模的周期較長,模具成本也比模內發泡模具高,而且該工藝的技術難度較高,后期調試周期較長,產品的綜合成本較高。模內發泡工藝的缺點是發泡劑較貴,產品的減重效果不是特別明顯,減重效果低于薄壁注塑工藝,物理發泡工藝和core-back工藝。

昆山PLA發泡定制
彈性體材料是指在受到外力或變形時,能夠恢復原狀或者接近原狀的材料。其最基本的特性就是彈性,即在受到一定的外力作用后能夠發生彈性變形,然后在去除外力后能夠自動恢復原狀的能力。因此,彈性體材料在工業制造、機械制造和航天、軍事等領域中扮演著重要的角色。 彈性體材料最典型的代表就是橡膠。橡膠具有較高的彈性和機械強度,具有良好的抗拉、抗壓、抗撕裂和耐磨性能,適用于制作各種密封圈、彈簧、橡膠管等重要的機械零部件。除了橡膠之外,還有許多其他的彈性體材料,例如聚合物材料、彈性泡沫等,這些材料都具有廣泛的應用領域。由于彈性體材料具有良好的柔韌性和粘性,因此可以用于制作各種居家用品、文具用品、玩具等。此外,彈性體材料還可以用于醫療領域中,例如制作假肢和支架等醫療器械。在軍事領域中,彈性體材料可以用于制造坦克履帶、防彈衣和車胎等軍事裝備,具有重要的戰略意義。彈性體材料是現代工業領域中不可缺少的一種材料,其廣泛應用于制造、機械、醫療、軍事等領域,為推動經濟發展和技術進步做出了巨大貢獻。隨著新技術和新材料的不斷涌現,相信彈性體材料的應用領域將會更加廣泛。 TPU材料(熱塑性聚氨酯)是一種由聚醚或聚酯多元醇和二異氰酸酯組成的熱塑性彈性體。它具有優異的彈性、耐磨性、耐油性、耐化學性、耐氧化性和良好的加工性能。由于其優異的物理和化學性質,TPU材料被廣泛應用于汽車、運動鞋、電子產品、醫療器械、玩具、建筑材料等領域。 POE材料是一種烯烴共聚物,其含量一般在20~50%之間。其優異的物理性質包括良好的伸展性、回彈性、耐磨性、耐撕裂性、防水性和耐氣候性等。此外,POE材料還具有良好的化學穩定性,可以在寬廣的溫度和化學介質條件下使用。這些性質使得POE材料在各種應用領域中具有廣泛的應用前景。其次,POE材料的制備方法分為物理法和化學法兩類。物理法主要是采用熔融混合或混合方式將多種材料混合熔融后制成,而化學法主要是采用聚合反應將不同單體聚合成共聚物。POE材料的物理和化學制備方法各有優缺點,具體制備方法應根據具體的應用要求而定。 TPEE材料(熱塑性聚酯彈性體)是一種由聚酯多元醇、二酸和丁二酸酯組成的熱塑性彈性體。它具有良好的彈性、耐磨性、耐油性、耐化學性、耐氧化性和耐高溫性能。由于其優異的性能,TPEE材料被廣泛應用于汽車、電氣電子、醫療器械、玩具、運動器材等領域。 彈性體材料的制造工藝十分多樣,其中最常見的方式就是熱壓模塑和擠出成型。在這些制造過程中,需要考慮材料的成型條件、工藝參數和結構設計等因素,以確保材料具有足夠的彈性和機械性能。隨著現代工業技術的不斷發展,在彈性體制造領域中也出現了許多新的制造技術和新材料,例如反應注塑、液相硅膠等,這些新技術和新材料大大拓寬了彈性體材料的應用領域。

昆山PLA發泡定制
年來綜合性能優異、可回收易降解的聚丙烯發泡材料已成為泡沫塑料家族中的“新寵”,是聚合物泡沫材料中增長速度快的品種。超臨界二氧化碳(CO2)發泡聚合物技術是制備聚丙烯微孔發泡材料的關鍵核心技術,近日華東理工大學化工學院趙玲教授團隊在該技術領域取得了實質性突破,成功開發了高性能聚丙烯微孔發泡材料綠色制備過程的優化和強化技術。聚合物發泡有物理發泡劑和化學發泡劑兩大類。化學發泡劑存在化學殘留、發泡過程難控制和不易獲得高發泡倍率等缺點;物理發泡劑中的氟氯烴類則對臭氧層有破壞作用,已逐漸被禁止和限制使用;而一些新型氟碳氫化合物的全球變暖潛能值仍相對較高,烷烴類發泡劑則易燃燒不安全。相比這些傳統的發泡劑,超臨界CO2發泡聚合物技術作為綠色制造技術,已被工信部列入我國優先發展的產業關鍵共性技術,而且CO2進入聚合物后會引起熔點、表面張力和黏度下降、結晶行為改變等一系列變化,可以制備微孔甚至納米泡孔材料。丙烯微孔發泡丙烯是結晶聚合物,低溫固態發泡受結晶限制,很難制備高發泡倍率產品;高溫發泡聚合物熔體強度不夠無法保持完整泡孔,可操作窗口窄。因,大規模制造具有穩定均勻泡孔形貌和外形尺寸的高發泡倍率微孔材料難度大。為了攻克這一難題,趙玲團隊聯合無錫會通、中石化北化院、浙江新恒泰、鎮海煉化等單位,在合適物料體系、可控工藝過程和高效工業裝備等方面開展了超臨界CO2發泡聚丙烯的優化、強化和工程化等系列工作,形成了“適合超臨界CO2發泡的聚丙烯專用料”“分步/分段發泡新工藝”“優化構建流場結構實現高效規模制備”三大技術創新。趙玲介紹,在低于流動溫度的可變形區發泡,既可突破結晶的制約,又能保證發泡材料微孔結構和外形尺寸穩定成型。基于這一發泡機制,他們開發了兼具較寬發泡溫度窗口和較強的CO2溶解擴散能力的聚丙烯發泡專用料,以及能改善泡孔結構和表觀形態的新型功能助劑/添加劑。CO2變壓飽和提高了過程效率和發泡倍率,氣泡成核和生長的分段實施減小了高壓設備體積;同時釜壓發泡、模壓發泡等高壓設備和聚合物預成型體的結構優化設計,保證了均勻的壓力場、溫度場和速度場,實現了低密度聚丙烯微孔發泡材料的規模制造和柔性生產。利用上述創新技術,項目團隊建設了2套年產3萬立方米模壓發泡裝置,實現了低密度聚丙烯微孔厚板的制造;新建了4套、優化改造了3套年產4萬~6萬立方米的釜壓發泡裝置,生產效率提高25%,成品率提高到99%以上,發泡專用料已在鎮海煉化生產,2016~2018年新增產值3.31億元、利稅1.09億元。此外,該團隊已獲得授權發明專利8件、實用新型專利8件;相關研究成果發表了46篇SCI/EI收錄論文。趙玲表示,超臨界CO2模壓發泡技術通用性強,除聚丙烯外,還可用于聚氨酯彈性體微孔發泡材料的生產,多種熱塑性聚合物及其復合材料的中試已經完成。采用該技術生產的聚丙烯發泡專用料,除可應用于汽車零部件和內飾、緩沖包裝等傳統領域,還可滿足兒童玩具、食品、醫療、家居用品等領域對綠色材料的需求。由于微孔賦予了聚丙烯獨特的性能,聚丙烯微孔發泡材料還可應用于更多的新興領域,如新能源汽車動力電池墊片、5G通信微波中繼天線罩、高檔汽車音響振膜、防彈衣背板等。

昆山PLA發泡定制
塑料化工研究發展至今,已合成出上千種高分子材料,其中具有工業價值的僅百余種,塑料常用的樹脂原料90%以上集中在五大通用樹脂(PE、PP、PVC、PS、ABS),目前再繼續合成大批新的高分子材料難度很大,既不經濟也不現實。在聚乙烯、聚丙烯塑料改性是目前高分子材料未來發展的一個重要領域,龍樸君整理了這部分的相關信息,供大家參考。深入研究聚合物組成、結構和性能的關系,并在此基礎上對現有的塑料進行改性,以制造適用的塑料新材料,已成為發展塑料工業的有效途徑之一,全球的改性塑料行業也因此在近年內獲得了長足的發展。關于改性的基礎知識在通用塑料和工程塑料的基礎上,通過物理、化學、機械等方式,經過填充、共混、增強等加工方法,改善塑料的性能或增加功能,對塑料的阻燃性、強度、抗沖擊性、韌性等機械性能得到改善和提高,使得塑料能適用在特殊的電、磁、光、熱等環境條件下。從原料樹脂的生產到多種規格及品種的改性塑料母料的生產,改性技術廣泛應用于幾乎所有的塑料制品的原材料與成型加工過程中。如塑料的外觀、透明性、密度、精度、加工性、機械性能、化學性能、電磁性能、耐腐蝕性能、耐老化性、耐磨性、硬度、熱性能、阻燃性、阻隔性等方面。為了降低塑料制品的成本、改善性能、提高功能,都離不開塑料改性技術。如何進行聚乙烯的改性?1、不同密度的聚乙烯的共混改性由于市場上的專用原料較少和供應的不平衡,促進了共混改性技術的發展。根據不同的吹塑中空制品的性能要求,可以通過調整低、高密度聚乙烯在配方中的不同比例來滿足要求。一般說來,小型制品、要求較軟的制品、盛放化學藥品、洗滌劑之類的容器,低密度聚乙烯的比例應該高些,高密度聚乙烯的比例應該低些。當然,并不是所有的低、高密度聚乙烯都能用于吹塑中空制品,應該從市場上選擇能用于吹塑的塑料材料,并通過改進配方設計,使制品的性能價格比達到優。2、不同分子量的高密度聚乙烯共混改性對于同為高密度聚乙烯材料來說,即使同為可用于吹塑成型的,可能在密度上相差無幾,但從分子量上來說,差別可能較大。樹脂牌號手冊上一般對材料的分子量都沒有標出,而從融體指數上大致可以看出。在擠出吹塑中空制品時,隨著所用吹塑級的分子量的提高,熔體強度會相應提高,同時制品的機械性能也會提高。但在實踐中發現,當分子量提高到一定程度后,熔體強度和擠出速率反而有下降的趨勢。出現這種情況后,對制品的正常生產將造成不同程度的負面影響,有時甚至會引發安全事故。制品加工時,出現分子量提高,熔體強度和擠出速率下降的情況,這與擠出機螺桿和進料段設計有較大的關系。雖然在設備上改進可以取得較為明顯的效果,但從材料配方上進行改進更能取得當期實效和減少設備改造的投資。將不同分子量、不同生產廠家生產的聚乙烯按比例共混,對于改善材料的分子量分布和材料內微量添加劑元素的分布大有好處。將它用于擠出吹塑, 往往容易收到較好的效果。從制品的化學性能,機械性能及生產中的各項工藝性出發,可以比較自由的設計出各種不同的配方,來滿足各種不同的要求,往往還可達到降低生產成本的目的。3、不同品種塑料的共混改性在工廠的現場生產當中,往往由于種種原因的限制,還會有許多不同的要求。比如說采用一些分子量較低的材料來代替分子量較高的塑料原料,不但是市場供應狀況的限制,還有可能是制造成本的要求,比如,在HDPE中加人一定量的PP,就能有效的改善的剛性,而且不會影響的沖擊強度。加入的比例需要根據產品的要求來確定。4、高密度聚乙烯的填充改性技術在加工塑料制品時,適當的加入各種不同的填充劑,不但可以提高塑料制品的剛度和硬度,同時也可以大幅度的降低原料成本。單就降低成本這點出發,對許多附加值低的產品來說,就值得作深入的研究。就近幾年來塑料制品加工廠填充改性的情況來看,技術層次普遍較低。