江蘇TPEE材料廠家
發布時間:2024-05-15 01:03:58
江蘇TPEE材料廠家
與傳統注塑制品相比,微孔發泡注塑制品具有質量更輕、翹曲和內部殘余應力更少、尺寸穩定性好、成型周期短等一系列優點。目前,欠注發泡成型是微孔注塑技術中應用為廣泛的工藝之一,具有操作簡單、效率高、能夠生產復雜制件,且能耗少,符合節約材料,降低成本這一發展理念,滿足發泡產品市場化的需求。然而,欠注發泡成型工藝也存在發泡制品內部泡孔易發生大量變形,泡孔尺寸分布不均勻,所得制品表面存在大量的氣痕、銀紋等缺陷,制約了其力學性能的提高和外觀視覺,阻礙了欠注發泡制品的進一步應用。國家復合改性聚合物材料工程技術研究中心的何力團隊采用自主研發的氣體反壓裝置,利用化學欠注發泡工藝研究氣體反壓(GCP)對微孔注塑過程中發泡行為的影響。研究發現,采用氣體反壓可以減少發泡注塑制品的泡孔變形以及不均勻等缺點,改善了泡孔的形態。實驗方法聚丙烯微孔發泡將PP、發泡劑(AC)、發泡助劑[Zn(St)2/ZnO]按照98.5∶1∶0.5的比例混合均勻后加入料筒中進行塑化。然后打開氣體反壓裝置,在型腔中分別注入固定的GCP為0,0.2,0.4,0.6,0.8 MPa的氣體,隨后按照表1的工藝參數注射熔融樹脂進行發泡,冷卻后,取出PP發泡樣品。GCP對充模過程中熔體壓力的影響熔體注射完后,熔體壓力瞬間達到值。隨著GCP從0增加至0.8 MPa,熔體內部壓力從1.55 MPa增大到2.16 MPa,注射完成后,隨著氣體的排出,熔體壓力瞬間下降,隨著冷卻收縮,熔體壓力逐漸趨于0 MPa。由此可知,GCP可以明顯地提高熔體充模過程中的熔體壓力,改善欠注發泡過程中的熔體壓力環境。 GCP對泡孔質量的影響在沒有施加氣體反壓時,由于熔體流動速率遠大于泡孔的膨脹速率,泡孔發生流動剪切變形,導致末端位置的泡孔在皮層區域受到剪切作用時間和作用力較大,在流動方向上出現很大的變形,泡孔發生撕裂合并現象,泡孔形貌極不規則,而中間區域的泡孔形態受到剪切力較小,呈現規整圓形形態。同時發現,隨著GCP的增大,皮層附近撕裂變形的泡孔區域變小,熔體內部芯層泡孔從橢圓形向規整圓形形態轉變,規則泡孔區域所占比例增大,泡孔之間呈現獨立分布。當GCP達到0.8 MPa時,皮層附近泡孔呈現出相對較好的圓形形態,此時整體泡孔的變形較小。這是因為GCP可以有效地降低泡孔在充模過程中受到的流動剪切作用,GCP值越大,泡孔在遷移過程中受到熔體壓力越大,泡孔受到熔體的約束力大,泡孔不易發生變形。GCP對泡孔結構參數的影響GCP對泡孔結構參數的影響如下圖所示。可知,在常壓下泡孔的非變形層(也就是規則泡孔區)厚度僅占整個樣品厚度的10.9%;隨著GCP的增大,泡孔的非變形層所占比例逐漸升高,GCP為0.8 MPa時,升高至26.7%。而泡孔變形層區域厚度所占比例隨著GCP的增大而大幅度下降,從63.7%下降到45.4%,這說明GCP可以減小泡孔變形層,增大規則泡孔區域范圍。對變形層的泡孔變形度進行統計,如下圖所示,泡孔的平均長度隨著GCP的增加,整體呈現減小的趨勢,泡孔的平均寬度隨著GCP的增加而逐漸增大,泡孔的變形度隨GCP的增大而減小,由常壓下0.530的泡孔變形度降低到GCP為0.8 MPa下的0.304泡孔變形度,即GCP可以減小泡孔長度與寬度的差距,使變形區的泡孔變形程度減小。對不同GCP下泡孔非變形層的泡孔直徑進行統計,見圖c,隨著GCP的增加,當GCP為0.2 MPa時泡孔直徑略有減小,但隨著GCP的進一步增大,泡孔直徑從36.09 μm增大到41.93 μm。這是因為GCP的增大使得熔體的壓力也隨之增大,使得泡孔的成核臨界能壘升高,泡孔的成核速率下降,泡孔在充模過程中受到流動場的影響減弱,更多的氣體在卸壓階段促進泡孔的生長,因此熔體壓力越大,泡孔直徑越大。GCP提高了充模時的熔體壓力,有效地降低了泡孔的變形,且隨著GCP的升高,泡孔直徑增大,泡孔密度下降,發泡材料的質量減少整體趨于不變。結論隨著GCP從0增加至0.8 MPa,熔體內部的壓力從1.55 MPa增大到2.16 MPa,使充模過程中受流動影響的泡孔數減小,減小了泡孔受到的流動剪切力。隨著GCP的增大,泡孔變形層區域厚度所占比例從63.7%下降到45.4%,變形層的泡孔的變形度從0.530下降到0.304,泡孔的平均長度增大。GCP的增加有效地改善了泡孔形貌,減小了泡孔變形層的CP增加了熔體流動時的阻力,提高了注塑充模階段的熔體壓力,使得臨界成核點后移,泡孔的成核長大在充模后進行,進而改善了制品泡孔的形貌。

江蘇TPEE材料廠家
與傳統注塑制品相比,微孔發泡注塑制品具有質量更輕、翹曲和內部殘余應力更少、尺寸穩定性好、成型周期短等一系列優點。目前,欠注發泡成型是微孔注塑技術中應用為廣泛的工藝之一,具有操作簡單、效率高、能夠生產復雜制件,且能耗少,符合節約材料,降低成本這一發展理念,滿足發泡產品市場化的需求。然而,欠注發泡成型工藝也存在發泡制品內部泡孔易發生大量變形,泡孔尺寸分布不均勻,所得制品表面存在大量的氣痕、銀紋等缺陷,制約了其力學性能的提高和外觀視覺,阻礙了欠注發泡制品的進一步應用。家復合改性聚合物材料工程技術研究中心的何力團隊采用自主研發的氣體反壓裝置,利用化學欠注發泡工藝研究氣體反壓(GCP)對微孔注塑過程中發泡行為的影響。研究發現,采用氣體反壓可以減少發泡注塑制品的泡孔變形以及不均勻等缺點,改善了泡孔的形態。丙烯微孔發泡實驗方法將PP、發泡劑(AC)、發泡助劑[Zn(St)2/ZnO]按照98.5∶1∶0.5的比例混合均勻后加入料筒中進行塑化。然后打開氣體反壓裝置,在型腔中分別注入固定的GCP為0,0.2,0.4,0.6,0.8?MPa的氣體,隨后按照表1的工藝參數注射熔融樹脂進行發泡,冷卻后,取出PP發泡樣品。GCP對充模過程中熔體壓力的影響熔體注射完后,熔體壓力瞬間達到大值。隨著GCP從0增加至0.8?MPa,熔體內部大壓力從1.55?MPa增大到2.16?MPa,注射完成后,隨著氣體的排出,熔體壓力瞬間下降,隨著冷卻收縮,熔體壓力逐漸趨于0?MPa。由此可知,GCP可以明顯地提高熔體充模過程中的熔體壓力,改善欠注發泡過程中的熔體壓力環境。CP對泡孔質量的影響在沒有施加氣體反壓時,由于熔體流動速率遠大于泡孔的膨脹速率,泡孔發生流動剪切變形,導致末端位置的泡孔在皮層區域受到剪切作用時間和作用力較大,在流動方向上出現很大的變形,泡孔發生撕裂合并現象,泡孔形貌極不規則,而中間區域的泡孔形態受到剪切力較小,呈現規整圓形形態。同時發現,隨著GCP的增大,皮層附近撕裂變形的泡孔區域變小,熔體內部芯層泡孔從橢圓形向規整圓形形態轉變,規則泡孔區域所占比例增大,泡孔之間呈現獨立分布。當GCP達到0.8?MPa時,皮層附近泡孔呈現出相對較好的圓形形態,此時整體泡孔的變形較小。是因為GCP可以有效地降低泡孔在充模過程中受到的流動剪切作用,GCP值越大,泡孔在遷移過程中受到熔體壓力越大,泡孔受到熔體的約束力大,泡孔不易發生變形。GCP對結構參數的影響CP對泡孔結構參數的影響如下圖所示。可知,在常壓下泡孔的非變形層(也就是規則泡孔區)厚度僅占整個樣品厚度的10.9%;隨著GCP的增大,泡孔的非變形層所占比例逐漸升高,GCP為0.8 MPa時,升高至26.7%。而泡孔變形層區域厚度所占比例隨著GCP的增大而大幅度下降,從63.7%下降到45.4%,這說明GCP可以減小泡孔變形層,增大規則泡孔區域范圍。對變形層的泡孔變形度進行統計,如下圖所示,泡孔的平均長度隨著GCP的增加,整體呈現減小的趨勢,泡孔的平均寬度隨著GCP的增加而逐漸增大,泡孔的變形度隨GCP的增大而減小,由常壓下0.530的泡孔變形度降低到GCP為0.8?MPa下的0.304泡孔變形度,即GCP可以減小泡孔長度與寬度的差距,使變形區的泡孔變形程度減小。對不同GCP下泡孔非變形層的泡孔直徑進行統計,見圖c,隨著GCP的增加,當GCP為0.2?MPa時泡孔直徑略有減小,但隨著GCP的進一步增大,泡孔直徑從36.09?μm增大到41.93?μm。這是因為GCP的增大使得熔體的壓力也隨之增大,使得泡孔的成核臨界能壘升高,泡孔的成核速率下降,泡孔在充模過程中受到流動場的影響減弱,更多的氣體在卸壓階段促進泡孔的生長,因此熔體壓力越大,泡孔直徑越大。

江蘇TPEE材料廠家
簡述聚丙烯微孔發泡新材料(Microcellular Polypropylene foam), 簡稱MPP,是特指泡孔尺寸小于100微米的聚丙烯多孔發泡材料(更嚴格地定義是泡孔尺寸小于10微米,泡孔密度大于10的9次方個/cm3)。由于材料內部大量微米級泡孔的存在,MPP具有優異的減震、緩沖、隔熱和吸聲等性能,可廣泛應用于包裝、交通工具、箱包、體育器材等領域,是傳統EVA、PU、PS發泡材料、EPE和EPP的替代物。聚丙烯微孔發泡性能與應用應用超臨界二氧化碳技術(supercritical carbon dioxide) 制備MPP,在高溫高壓下將二氧化碳氣體導入聚丙烯材料基體,并誘導其成核、發泡,形成含有大量微米尺度泡孔的微孔發泡材料。發泡過程清潔無污染,發泡制品衛生環保。發泡過程PP材料未發生交聯,因此可回收循環使用。丙烯(PP)本身是無毒材料,是目前嬰兒奶瓶和可微波加熱餐盒的常用材料。清潔衛生的MPP特別適合于醫療器械、食品等包裝材料衛生等級要求較高的領域。也可應用于兒童拼圖、玩具等對產品健康要求較高的領域,代替常用的由AC發泡劑制造的交聯PE泡沫,EVA泡沫。PP是半結晶聚合物,其熔點一般150~170℃。相比于耐溫只有70~80℃的PE、PS、PU發泡材料,MPP的使用溫度可達120℃,因此MPP特別適合高溫包裝、高溫保溫等領域。MPP集增強、隔熱和降噪為一體,也特別適用于對材料輕量化要求較高的領域,如汽車、軌道交通,船舶,風機葉片等。輕質高強的MPP厚板作為結構泡沫使用,代替傳統的結構泡沫如PVC/PU互穿結構泡沫、PET結構泡沫等,特別是作為三明治夾芯復合材料的芯材使用。MPP微米尺度的泡孔賦予材料的特別之處有:(1) 同等發泡倍率(或表觀密度)下,由于泡孔較小,微孔發泡材料的機械性能損失較小。這意味著使用MPP可以更加節約材料,更加降低制品重量和體積。2) 由于泡孔尺寸在1-100μm之間可控,MPP可以被剖切成厚度小于0.1mm的超薄片材,而片材表面不會穿孔,可應用于微電子器件的包裝。(3) 由于表面大量微米級泡孔的存在,MPP適合作為液晶顯示器背光模組的反射板,提高漫反射率。(4) 微米尺度的泡孔有效降低了泡孔內氣體的對流,從而有效降低了由空氣對流引起的熱傳遞。因此高倍率的微孔發泡材料具有較低的、依賴于泡孔結構的長期穩定的低導熱系數。(5) 輕質高強的MPP片材適合于作為揚聲器振膜使用。(6) 同樣由于其微米尺度的泡孔,MPP具有極佳的表面保護性能,可應用于液晶面板等防護性要求較高的包裝領域。
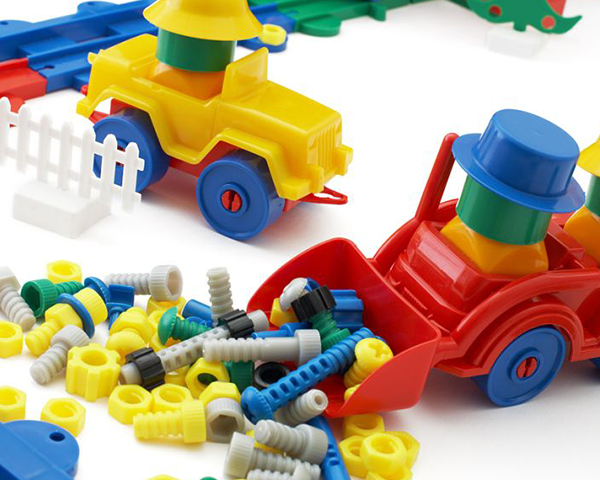
江蘇TPEE材料廠家
年來綜合性能優異、可回收易降解的聚丙烯發泡材料已成為泡沫塑料家族中的“新寵”,是聚合物泡沫材料中增長速度快的品種。超臨界二氧化碳(CO2)發泡聚合物技術是制備聚丙烯微孔發泡材料的關鍵核心技術,近日華東理工大學化工學院趙玲教授團隊在該技術領域取得了實質性突破,成功開發了高性能聚丙烯微孔發泡材料綠色制備過程的優化和強化技術。聚合物發泡有物理發泡劑和化學發泡劑兩大類。化學發泡劑存在化學殘留、發泡過程難控制和不易獲得高發泡倍率等缺點;物理發泡劑中的氟氯烴類則對臭氧層有破壞作用,已逐漸被禁止和限制使用;而一些新型氟碳氫化合物的全球變暖潛能值仍相對較高,烷烴類發泡劑則易燃燒不安全。相比這些傳統的發泡劑,超臨界CO2發泡聚合物技術作為綠色制造技術,已被工信部列入我國優先發展的產業關鍵共性技術,而且CO2進入聚合物后會引起熔點、表面張力和黏度下降、結晶行為改變等一系列變化,可以制備微孔甚至納米泡孔材料。丙烯微孔發泡丙烯是結晶聚合物,低溫固態發泡受結晶限制,很難制備高發泡倍率產品;高溫發泡聚合物熔體強度不夠無法保持完整泡孔,可操作窗口窄。因,大規模制造具有穩定均勻泡孔形貌和外形尺寸的高發泡倍率微孔材料難度大。為了攻克這一難題,趙玲團隊聯合無錫會通、中石化北化院、浙江新恒泰、鎮海煉化等單位,在合適物料體系、可控工藝過程和高效工業裝備等方面開展了超臨界CO2發泡聚丙烯的優化、強化和工程化等系列工作,形成了“適合超臨界CO2發泡的聚丙烯專用料”“分步/分段發泡新工藝”“優化構建流場結構實現高效規模制備”三大技術創新。趙玲介紹,在低于流動溫度的可變形區發泡,既可突破結晶的制約,又能保證發泡材料微孔結構和外形尺寸穩定成型。基于這一發泡機制,他們開發了兼具較寬發泡溫度窗口和較強的CO2溶解擴散能力的聚丙烯發泡專用料,以及能改善泡孔結構和表觀形態的新型功能助劑/添加劑。CO2變壓飽和提高了過程效率和發泡倍率,氣泡成核和生長的分段實施減小了高壓設備體積;同時釜壓發泡、模壓發泡等高壓設備和聚合物預成型體的結構優化設計,保證了均勻的壓力場、溫度場和速度場,實現了低密度聚丙烯微孔發泡材料的規模制造和柔性生產。利用上述創新技術,項目團隊建設了2套年產3萬立方米模壓發泡裝置,實現了低密度聚丙烯微孔厚板的制造;新建了4套、優化改造了3套年產4萬~6萬立方米的釜壓發泡裝置,生產效率提高25%,成品率提高到99%以上,發泡專用料已在鎮海煉化生產,2016~2018年新增產值3.31億元、利稅1.09億元。此外,該團隊已獲得授權發明專利8件、實用新型專利8件;相關研究成果發表了46篇SCI/EI收錄論文。趙玲表示,超臨界CO2模壓發泡技術通用性強,除聚丙烯外,還可用于聚氨酯彈性體微孔發泡材料的生產,多種熱塑性聚合物及其復合材料的中試已經完成。采用該技術生產的聚丙烯發泡專用料,除可應用于汽車零部件和內飾、緩沖包裝等傳統領域,還可滿足兒童玩具、食品、醫療、家居用品等領域對綠色材料的需求。由于微孔賦予了聚丙烯獨特的性能,聚丙烯微孔發泡材料還可應用于更多的新興領域,如新能源汽車動力電池墊片、5G通信微波中繼天線罩、高檔汽車音響振膜、防彈衣背板等。

江蘇TPEE材料廠家
核心技術優勢:1、技術創新:·成套設備:自主研發的超臨界CO2微孔發泡成套裝備,將化學工程的技術手段應用于聚合物加工。·適用性好:工藝適用于多種聚合物材料的微孔發泡(PP、PA、TPU、TPAE、PVDF…)。·控制確:通過宏觀工藝參數(溫度、壓力)的確控制,實現了對泡孔結構的確控制。2、性能優勢:·多類別:從彈性體到工程塑料的多種聚合物輕量化材料產品 。·高性能:充分發揮多孔結構作用能并配合材料的功能化改性,實現材料的高性能化 。·輕量化:低密度(min) 30kg/m3 。重環保:純物理發泡,制程清潔環保,產品安全無毒。聚丙烯微孔發泡已實現量產的產品種類:1、M-PP:聚丙烯微孔發泡板材2、M-PVDF:聚偏氟乙烯微孔發泡板材3、M-PA12:尼龍12微孔發泡板材4、M-TPU:熱塑性聚氨酯彈性體微孔發泡板材5、M-TPEE:熱塑性聚酯彈性體微孔發泡板材6、M-PEBA:熱塑性聚酰胺彈性體微孔發泡板材

江蘇TPEE材料廠家
摘要:長玻纖增強聚丙烯材料(PP-LGF)作為一種輕質高強的復合材料,在滿足汽車零部件性能的同時,對零部件減重具有明顯貢獻,目前在汽車零部件應用上備受青睞。文章主要介紹了PP-LGF在汽車儀表板輕量化方面的應用和發展現狀,詳細介紹了薄壁注塑、物理發泡、化學發泡三種成型工藝實現儀表板輕量化的技術概況,并展望了PP-LGF在儀表板上的應用前景。聚丙烯微孔發泡近年來,隨著我國經濟的不斷發展,汽車工業也得到了快速發展。然而,由此引發的環境問題也日益嚴重,通過汽車輕量化來降低油耗從而降低環境污染,已經成為汽車行業的研究熱點,其中,使用質量更輕的非金屬材料替代傳統金屬材料的研究在近年來也取得了較大進展。運用復合材料來部分取代車身結構件及內、外飾裝飾件是汽車輕量化的一種行之有效的方法。在眾多的復合材料中,長玻纖增強聚丙烯材料(PP-LGF)以其低廉的價格、優良的力學性能和環境友好性而獲得更多的青睞。與短玻纖增強聚丙烯材料(PP-SGF)相比,PPLGF在強度、剛度、翹曲度、耐疲勞、缺口沖擊強度和尺寸穩定性等方面更具優勢,因此,使用PP-LGF生產的汽車零部件可進一步實現重量及成本的降低。1 長玻纖增強聚丙烯材料性能特點長玻纖增強聚丙烯材料的制備工藝主要分為5種,即熔融浸漬、溶液浸漬、粉末浸漬、纖維混編工藝以及薄膜疊層工藝,而在汽車零部件領域主要應用的為熔融浸漬法。熔融浸漬法生產的PP-LGF粒子的長度一般為8mm~15mm,其中玻纖的含量可達20%~60%,粒子中玻纖的保留長度可達1mm~3mm,如圖1所示,相較于玻纖保留長度僅為0.2mm~0.4mm的PP-SGF材料,PPLGF因其內部纖維構成的三維網絡結構,可保證產品具有更優的力學性能、抗沖擊性能、耐蠕變性能等特點,更加適合應用于汽車領域對結構性能要求較高的零部件。此外,隨著纖維含量的增加,PP-LGF的性能也隨之提高。長玻纖增強聚丙烯材料在儀表板上的應用儀表板是汽車內飾中的重要部件,為提升汽車內飾的感知質量,中、高檔車型普遍會采用軟質儀表板,即在儀表板骨架表面增加軟質表皮層。儀表板骨架作為儀表板系統的主體部件,同時也是電器件和其他功能件的承載結構,因此要求其具有高強度及高剛性,目前在儀表板骨架上使用為廣泛的為PP材料,采用相同密度的PP-LGF材料替代傳統PP材料,在滿足相關性能的同時,可提升儀表板吸能性能,同時可將現有儀表板骨架的設計厚度由3mm~3.5mm降低到1.8mm~2.5mm,從而降低儀表板骨架重量,推動汽車內飾輕量化。以下將從PP-LGF應用于儀表板上的薄壁注塑、物理發泡、化學發泡三種成型工藝方面,介紹PP-LGF在儀表板輕量化方面的應用。 2.1 薄壁注塑薄壁注塑工藝是直接將產品壁厚減薄,在模具中進行加工的一種成型方法,與傳統PP材料注塑的3mm~3.5mm壁厚的儀表板骨架相比,PP-LGF材料運用薄壁注塑工藝制造的儀表板骨架產品壁厚一般為2.5mm左右,整體減重可達約25%。該工藝的投入成本較低,重量優勢明顯。目前,該工藝在國內和國外合資品牌中,如吉利、大眾、上汽、福特等均有應用,一般選擇PPLGF20材料,設計的產品壁厚一般為2.2mm~2.5mm。然而,薄壁注塑工藝也存在兩點問題,首先是該工藝的模具成本較高,使用薄壁注塑,成型模具需要采用熱流道設計,熱流道模具的成本要比普通注塑工藝的模具成本高。其次,注塑工藝管控和注塑精度要求高,因為PP-LGF中長玻纖分布的各向異性,采用PP-LGF材料的薄壁注塑產品翹曲變形較為嚴重,尺寸穩定性較差。2.2 物理發泡物理發泡工藝又稱為MuCell 工藝,它是以熱塑性材料為基體,通過將超臨界流體(二氧化碳或氮氣) 溶解到熱熔膠中形成單相溶體,并保持在高壓力下,然后,通過開關式射嘴射進溫度和壓力較低的模具型腔,由于溫度和壓力降低引發分子的不穩定性從而在產品內部形成從十到幾十微米不等的封閉氣泡微孔[4-5],該項技術早期由麻省理工學院發明,1995年由美國Trexel公司將技術實現全球商品化。MuCell 工藝優勢為成型周期短、產品尺寸穩定性好、翹曲低、產品輕量化和工藝適用性廣。MuCell工藝使用超臨界流體,可有效降低PP-LGF材料黏度, 提高熔體流動性。泡孔成長壓力代替傳統注塑中的保壓階段,縮短成型周期,同時,可使壓力分布均勻,有效降低PPLGF產品內應力,降低因長玻纖各項異性導致的產品翹曲,增加產品的尺寸穩定性。另外,泡孔填充可有效避免產品表面縮痕,微孔結構擴充,降低材料密度,產品重量減輕,較同材質實體,重量可降低5%~10%。目前,福特新蒙迪歐在儀表板骨架上應用了該工藝,骨架產品設計壁厚2.4mm,相較于實心材料重量降低了10%,此外,長城和大眾也有應用于此項技術。MuCell 工藝的缺點是一次性投入高,工藝難度大,同時相關研究表明,使用該工藝對儀表板減重比控制在3%~8%時,產品性能會下降10%左右,基本滿足性能要求,減重超過8%,機械性能和耐熱老化性能急劇下降,不能滿足要求。若使用MuCell 工藝推薦減重比為3%~5%。2.3 化學發泡化學發泡工藝包括模內發泡工藝和二次開模發泡工藝(core-back),二者均是在注塑過程中,利用塑料粒子中加入的碳酸氫鈉和碳酸銨類的無機發泡劑,受熱分解產生的二氧化碳等氣體,使產品形成微孔發泡結構,以降低材料密度,減輕產品重量。其中,core-back工藝因使用了二次開模,相較于模內化學發泡,發泡的倍率更高,產品中形成的泡孔數量更多,產品的減重比更大。一般來說,模內化學發泡的減重比相比于實心材料在5%~8%左右,而core-back工藝可高達30%~50%,具體根據退模行程決定。同物理發泡工藝一樣,化學發泡工藝可在PP-LGF材料應用減重的同時,減少產品翹曲變形,提升產品穩定性,而且二次開模發泡工藝能夠適用于做外觀件。目前,寶馬5系已在儀表板骨架上應用了PP-LGF的core-back工藝,產品壁厚由初始1.8mm左右發泡到3.8mm,重量降低了約40%,此外大眾的部分車型也已使用模內化學發泡工藝。core-back工藝的缺點是發泡劑較貴,開模的周期較長,模具成本也比模內發泡模具高,而且該工藝的技術難度較高,后期調試周期較長,產品的綜合成本較高。模內發泡工藝的缺點是發泡劑較貴,產品的減重效果不是特別明顯,減重效果低于薄壁注塑工藝,物理發泡工藝和core-back工藝。